Automotive
Solutions for the eMobility
The high quality and safety requirements in the automotive industry demand high standards on plastic materials. BASF’s broad portfolio - led by versatile and sophisticated polyamides (Ultramid®), polybutylene terephthalates (Ultradur®), polyphthalamides (PPA), and the specialty plastics polyoxymethylene (Ultraform®) and polyethersulfone (Ultrason®), offers solutions to keep pace with car manufacturers’ latest developments, while also setting innovative trends. Technical properties and high functionality are key here. We have set up a global expert team on that topic.
Thermoplastics solutions for the eMobility
Ultradur®, the polybutylene terephthalate (PBT) from BASF, has a specific combination of properties making it an ideal material for particular use in eMobility and other electrical engineering and electronics applications.
Long lasting under tough conditions
Ultradur® shows not only high stiffness and good thermal resistance but also exceptional dimensional stability, constant electrical properties and thermal performance. As well it offers excellent color stability at elevated temperatures, and therefore makes orange a longlasting signal color.
Flame-retardant PBT has hitherto almost always used halogenated flame retardant systems. As new requirements, e.g. high CTI values, have to be fulfilled BASF developed several Ultradur® grades with non halogenated flame retardancy.
To allow our customers the production of connectors for a use at elevated temperatures and high humidity, BASF also set up some hydrolysis resistant (HR) grades. The main feature of the Ultradur® product range with the suffix HR (=hydrolysis resistant) is the extremely high resistance of the PBT polymer (PBT=polybutylene terephthalate) to damage due to water at elevated temperatures. Contact with water in polyesters, even in the form of atmospheric humidity, leads to hydrolytic cleavage of the polymer chains and thus to a weakening of the material properties, particularly at elevated temperatures. Ultradur® HR is based on standard PBT, but incorporates highly effective additives which greatly retard the hydrolytic degradation and can therefore considerably extend the life of a part.
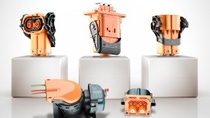
Meeting new requirements of the eMobility industry
For critical applications such as those in automotive electronics, long life and reliability are basic requirements. Connectors in an electric car have to withstand up to 1000V, which is even more challenging. The PBT used for these connectors needs to fulfill these demanding conditions guaranteeing safety as much as possible. To immediately identify the high voltage parts under the hood they need to be manufactured with a product which is colorable in orange RAL 2003. This color needs to be long-lasting even at elevated temperatures. Compared to PA, Ultradur shows up a very low yellowing effect but even more stable coloring.
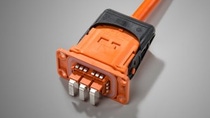
Naturally, the plastic parts should be functional in all climate zones on earth, even in damp hot conditions. If spray water and road salt play a role, this can also increase the demands on the plastic. Therefore, the level and duration of the stress are key factors as to whether or not an application is feasible using a PBT without improved hydrolysis resistance.
Today, the specifications for a number of plastic applications in the automotive sector include tests at elevated temperatures and humidity or tests on changing climatic conditions. These tests can only be passed by HR-modified PBT grades.
Ultradur® HR Technical details
Engineering plastics for the eMobility
EMI-shielding for high-voltage housings
For high-voltage (HV) housings in electric cars, Ultramid® A3U42G6 and Ultramid® B3U50G6 meet the high standards on flame retardance, mechanics, and electrical isolation. Thus, they allow automotive manufacturers to save on weight and design space while being an alternative to standard aluminum die-cast solutions.
For being a real alternative in such HV applications, plastic materials must convince with equal or better performance compared to metal components. This includes a solution for electromagnetic shielding (EMI-shielding), which is an intrinsic property of metallic structures. In this context, BASF is working on processes to equip such plastic housings made of flame-retardant Ultramid® with a thin metal layer. The same high EMI-shielding efficiency can be obtained from this method as with housings made of pure metal. However, the plastic solution provides a weight reduction potential and is highly cost-effective versus aluminum die-cast. In addition, the advantage of the plastic for functional integration can be fully exploited.
Solutions for battery components
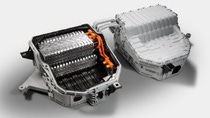
Many eMobility solutions can only be implemented reliably and efficiently by using highly versatile plastics. For the dynamic market of electric and hybrid vehicles, BASF is expanding its range of engineering plastics and polyurethane systems. The key to the success of electromobility will be how quickly the performance, capacity, weight, safety, reliability and above all these, the manufacturing costs and economic efficiency of the battery systems can be further improved.
Optimized Ultramid® A grades can make a vital contribution to complex automotive cooling systems, while new eMobility coolants, like BASF’s Glysantin®, can trigger new challenges for plastics. For this reason, engineering plastics and Glysantin® experts at BASF are working closely together to optimally adapt future plastics solutions to the coolants of tomorrow.
Moreover, Ultramid® B can be used for battery cell frames or pressure end plates to reduce weight in battery systems. Ultradur® offers excellent properties for electronic control units such as battery management systems. All material solutions optimize the battery system and enable an economically viable mass production.
Fuel Cell
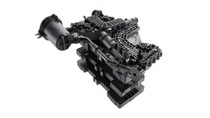
Alongside the continued development of cars with more efficient internal combustion engines, chemistry is making an important contribution to a number of different electric drive concepts. Further progress is also being made in the field of fuel cells. For the Mercedes GLC F-Cell, it is the all-round excellence of Ultramid®’s properties that counts: good thermal and chemical resistance, dynamic stiffness, impact strength, and good long-term performance.
In view of the unique material structure, and on the basis of intensive material analyses of the chemical and mechanical resistance, tailor-made Ultramid® grades A3WG10 CR and A3EG7 EQ are used in fuel cell components. Two glass fiber-reinforced Ultramid® grades are being used as standard to manufacture the anode- and cathode-end plate. Ultramid® A3EG7 EQ is an ideal material, given the exceptional purity requirements associated with sensitive applications in the electronics industry. In the case of the media distribution plate and the water separator unit, which is exposed to a wide variety of media through the cooling water, air and hydrogen channel, this Ultramid® grade offers excellent resistance, while at the same time meeting all requirements regarding the purity of the material.
Fellow engineers, automotive and electric car fans, high voltage connector specialists and plastic interested ones if you want to learn more about our eMobility plastic solutions from our:
European E&E specialists: Christina Zimmermann, Andreas Nixdorf, Roman Bem, Thomas Bayerl and Timo Prenzer. Reach out to our experts via contact form.
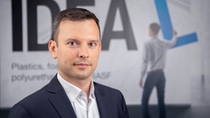
Roman Bem
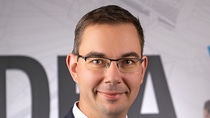
Thomas Bayerl
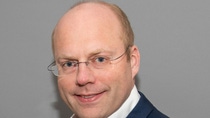
René Holschuh
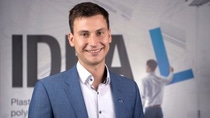
Andreas Nixdorf
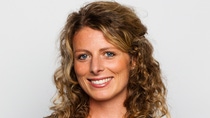
Christina Zimmermann
E&E specialists in Asia Pacific:
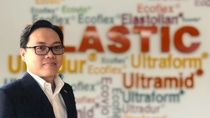
Swee Jin Saw
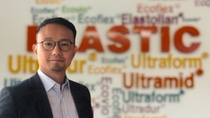
Hill Gu
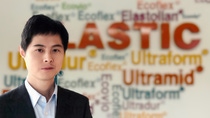
Jason Zhang
E&E specialists in North America:
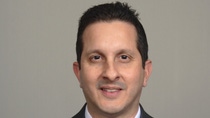
Brian Vargo
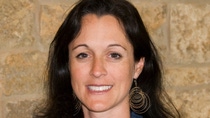
Lynn Ideker
Recharge yourself
See how BASF's innovations in battery materials inspired a global film competition and why we're optimistic about the future of eMobility.
Disclaimer
The data contained in this publication are based on our current knowledge and experience. In view of the many factors that may affect processing and application of our product, these data do not relieve processors from carrying out own investi-gations and tests; neither do these data imply any guarantee of certain properties, nor the suitability of the product for a specific purpose. Any descriptions, drawings, photographs, data, proportions, weights etc. given herein may change without prior information and do not constitute the agreed contractual quality of the product. It is the responsibility of the recipient of our products to ensure that any proprietary rights and existing laws and legislation are observed. (June 2013)