Performance Polymers
Autofroth®: A solution founded on versatility
BASF Autofroth® rigid polyurethane foam systems are specially formulated to meet and exceed customer needs in numerous applications including but not limited to commercial refrigeration, marine, and refrigerated trucking (reefer). With Autofroth®, BASF has created high-performing foam systems that are straightforward to setup and operate, cost-effective, tunable, and environmentally sustainable.
A streamlined system
Autofroth® are two-component polyurethane systems dispensed under low pressure using BASF equipment. Each component is “pumped” with nitrogen pressure through a specially designed dispensing gun, at a desired ratio, to create a foam that’s consistent in texture and pattern.
There are several benefits that come with using Autofroth®.
First, its ease of setup and processing. Thanks to the system’s simplicity, and the tools on offer to administer that, it’s more competitive than other high-pressure systems with high investment costs.
The way the components are shipped is another benefit that helps streamline initial start-up. “We provide Autofroth® foam systems in BASF-owned returnable steel cylinders or tanks,” says Dr. Mark Swartzlander, Autofroth Market Segment Manager at BASF. “That’s advantageous for example, as it eliminates the need to pay to dispose of a tote.”
We have a very strong technical team that’s able to support on both the chemistry side and equipment side to fine-tune formulations, set up equipment, and help customers troubleshoot.
Swartzlander adds that BASF provides a full end-to-end solution and are experts in the Autofroth® chemistry and equipment. “We’re selling high-quality performance foams, which is dispensed through BASF-sold equipment.”
The approach is conscious of the environment too. Not only do the returnable tanks reduce waste, but BASF has embraced the shift from hydrofluorocarbon (HFC) to hydrofluoroolefin (HFO) by offering blowing agents with low global warming potential and zero ozone depletion.
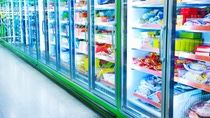
Proven possibilities
Thanks to its chemistry, Autofroth® provides a vast amount of design freedom, and its properties can be customized to solve a specific need or challenge. As Swartzlander says, “we have flexibility to fine-tune the foam’s properties, such as the density, reactivity, compressive strength, and/or thermal conductivity.”
Because of these possibilities, Autofroth® is used in all manner of applications, including insulating different designs of commercial refrigerators and within refrigerated trucks, or as flotation or structural foam for marine applications. It is also used in a host of other applications such as coolers, mannequins, and low-cost furniture. “BASF knows the full process, including the chemistry and dispensing equipment,” Swartzlander continues. “We can work with customers to find the right foam system to meet their needs and challenges.”
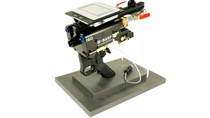
Dispensing results
To complement the chemistry of the high performing foam, BASF sells Autofroth® dispensing equipment. The incumbent Autofroth® SL3 Series Dispensing Gun offers a consistent shot size and adjustable flow controllers to easily apply Autofroth® regardless of the end application.
This year will also see the release of the Autofroth® Vortex Dispensing Gun, an updated model with improved ergonomics, mixing efficiency, and the option to integrate it with human machine interface (HMI).
“With both dispensing guns, we can control the ratio of the two components,” says Swartzlander. “Whether it’s dispensed as a 1:1 mixture or something different, it can be fine-tuned depending on the needs of the system.”
BASF also sells the Autofroth® TM-15 Timer/Ratio Monitor to be used in conjunction with the dispensing guns to set the programmability. For example, the user could program dozens of different shots based on volume, weight, or time. The TM-15 can also collect important quality control data along the way.
A complete package
Thanks to customizable chemistry, a selection of dispensing guns to seamlessly administer that chemistry, and additional BASF equipment to help optimize the process, Autofroth® is a holistic solution that offers a cost-effective alternative to conventional high-pressure rigid polyurethane foam systems.
“We have a very strong technical team that’s able to support on both the chemistry side and equipment side to fine-tune formulations, set up equipment, and help customers troubleshoot.” says Swartzlander.