Performance Polymers
Cellasto® Services: More than just a material provider
When you work with our team, you have access to a large portfolio of materials with varying capabilities. This includes Cellasto®, a dynamic, resilient material available in a range of grades to suit multiple purposes and budgets.
A fully certified Tier 1 supplier for both industry and automotive customers, when you work with BASF Cellasto®, you get more than just materials. You gain a complete engineering package and the quick development, innovative testing and quality standards that come with it, including:
- Simulation to predict product behavior
- Up-to-date physical validation through various tests
- Quality certifications, including environmental
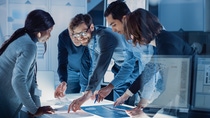
Why innovators choose Cellasto®
Cellasto® is a microcellular polyurethane elastomer that provides superior noise, vibration and harshness (NVH) reduction compared to rubber, plastic and other elastomers and is used in a wide range of applications and industries.
In automotive and independent aftermarket applications, this dynamic polyurethane foam’s high compressibility with low lateral expansion results in smaller, lightweight components.
The outstanding abrasion and environmental resistance of Cellasto® — including ozone and temperature — allow innovators to produce dynamic, durable components while maintaining a high level of design freedom.
We offer this unique material in a range of grades to suit different budgets and purposes, from premium to economy. We even offer compact, non-foam material solutions for components, such as subframe mounts. This material still allows you to reap some of the benefits of a microcellular polyurethane, including improved NVH performance and abrasion resistance.
Cellasto® testing capabilities
BASF offers its customers worldwide test support at five locations. The testing capabilities include static and dynamic tests of components and subsystems. We accompany the entire development process from the initial concept idea with a load/deflection curve up to tests for series release.
Static testing
The static tests are primarily used to record the component characteristics, which are also used to assess the deformation behavior. Other static tests include the measurement of the permanent-set and overload tests. Different environmental conditions such as temperature and humidity can be considered. Moreover, we are able to validate assembly and disassembly forces in order to guarantee tight fittings of all components. We also offer mounting and demounting tests to determine the amount of force required to either seat the jounce bumper within the cup or remove it from the cup as well as the force applied to the rod for rod-hugging jounce bumpers that do not mount to a cup.
Dynamic testing
Drop testing
The drop-test is an energy-controlled test method. Both speed and energy input can be controlled by the drop height and weight. As a result, a force/displacement hysteresis is obtained for each drop cycle, which serves as the basis for the subsequent evaluation. With drop speeds of up to 4m/s, the BASF test lab can apply high speed impact stress.
Hydropulser/ Shaker
BASF has capabilities for uniaxial and multiaxial testing with linear and torsional actuators.
Fatigue-Testing
Our hydropulsers enable both force- and displacement-controlled tests to evaluate the fatigue strength of parts and components. According to customer specifications, testing is performed using synthetic or real signals. Different environmental conditions such as temperature and humidity can be considered.
Dynamic characterization
For the dynamic characterization of the components, BASF has hydraulic and electromagnetic test benches available. The excitation signals can be applied as real or synthetic signals, different frequencies can be controlled as sweep or discrete single points, this can be force-, displacement- or acceleration-controlled. The dynamic characteristic values are evaluated by analyzing the hystereses.
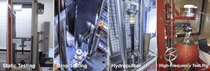
Simulation capabilities
With more than 25 years of experience in application and theory, simulation is an integral part of our development process and is part of our digital competencies.
Our expertise is particularly strong in material mechanics and microcellular polyurethanes (MCU) modeling, as well as structural analysis through non-linear FEA (Finite Element Analysis).
Our technology, combined with the expertise of our CAE analysts, ensures that simulation serves to benefit the entire development process, resulting in Cellasto® products designed by BASF for high-performance applications.
Benefits of BASF Cellasto® Advanced Simulation Techniques
Using our research as well as leading software packages for non-linear FEA, BASF has developed advanced methodologies tailored to the specific needs of Cellasto® and its wide range of applications.
Our simulation process accelerates the development phases by reducing the number of physical prototypes and amount of testing. In some cases, development cycles can even be skipped, enabling us to respond more quickly to our customers.
By using our FEA simulation methodologies in structural analysis, our CAE analysts can provide valuable information for Cellasto® product design, such as:
-
analysis of deformation behavior, including stability, contact and collision
-
load-deflection-characteristic and stiffness
-
stress/strain-analysis for assessment of local material loading and strength
-
reaction forces on assembled parts
Since proof of concept is possible without real prototypes, the BASF team can focus on product performance and quality from the start. Within virtual design loops, we can adopt and optimize product design to best fulfill your requirements.
Our methodology even outperforms classical design methods due to its ability to provide insight that is not available by means of any other experimental technique, such as with physical tests that would be too large or too complex to be realized within the confines of a test lab.
Quality Certificates
As leaders in green manufacturing, with more than 100 customers worldwide, adhering to strict safety, quality and environmental standards is a top priority. In addition to our long, successful track record in these areas, we have the following certifications:
IATF (International Automotive Task Force) 16949 Certification
-
Requirement of Tier 1 Suppliers
-
Ensures OEM quality is upheld
ISO 14001 Certification
-
Environmental focus
-
Includes CO2 emissions standards
RCMS Responsible Care Management System
-
Internal, broad BASF certification
-
Ensures that we consistently produce environmentally conscious, safe products
ISO 45001 Safety
-
Occupational health and safety management system and use
-
Provide a safe, healthy work environment through by preventing workplace injury and illness
-
Take active steps to improving the company’s OH&S performance
ISO 50001 Energy
-
Improve and conserve energy use through an energy management system
-
Create policies and use data to measure effectiveness for continuous improvement