Performance Polymers
Carbon management and circularity go hand in hand
Our society must remain healthy and livable for the future generations. For BASF, it translates into a commitment to reach net zero carbon emissions by 2050. This ambitious goal requires a reduction of fossil feedstock usage and plastics waste.
How can circular solutions contribute to this reduction?
First, the energy required to produce any materials (virgin or not) should come from renewable energy. It means replacing fossil fuels with green energy sources such as wind or solar. Secondly, we must keep fossil carbon in the ground. We should not only stop plastics waste, but also make sure that anything that can be recycled is actually recycled. For that, different technologies must be used in parallel.
Materials need carbon
Decarbonizing energy requires energy from renewable sources such as solar and wind. They are essential to make our plants run on green energy. Since our materials are carbon-based, the transition to circular carbon is the imperative step to prevent the use of additional fossil resources. This circular carbon can be obtained from different sources such as: biomass, CO2 and recycling of carbon containing waste streams. By combining renewable energy with circular carbon, we minimize the demand for new fossil carbon, hence contributing to CO2 emissions reduction.
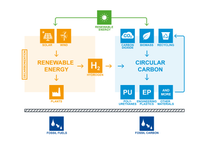
Electrolyser in Ludwigshafen
BASF plans 54MW electrolyser at its German headquarters to help decarbonise its operations and learn about the technology.
BASF is a pioneer is gas treatment technology
A CO2 capture process, jointly developed by Linde, Heidelberg Materials, and BASF, and based on BASF’s advanced OASE® blue technology, will be used for the first time at a large-scale CO2-capture facility operated by Capture-to-Use. The plant will be the world’s first industrial-scale carbon capture and utilization (CCU) facility. Around 70,000 tons per year of CO2 will be captured, purified and liquefied.
Biomass Balance approach
BASF has broken new ground with the development of the biomass balance process for the use of renewable raw materials in the chemical industry. This approach allows fossil raw materials to be replaced by renewable raw materials in BASF's Production Verbund.
Solar farm in Schwarzheide
On 25 August 2022, BASF enviaM commissioned the first joint solar farm with around 52,000 photovoltaic modules and a transformer station on an area of 24 hectares to supply green electricity to BASF.
Offshore wind farm Hollandse Kust Zuid
The subsidy-free offshore wind farm is expected to become fully operational in 2023. It will be the largest offshore wind farm in the world with a total installed capacity of 1.5 gigawatts.
Circular performance materials
At BASF, we co-create solutions with customers. We can provide a significant share of our portfolio as mass balanced products for which fossil feedstock has been replaced by non-fossil alternatives.
Recycling
Recycling prevents that existing carbon is released in the atmosphere by making it circular. All recycling technologies must be considered.
Global plant network benefitting from renewable energy
Our high-performance plastics are produced around the globe in plants with access to renewable energy.
Own company for renewable energy
BASF is bundling its activities in renewable energies under the umbrella of BASF Renewable Energy GmbH as of January 1, 2022.
From fossil to circular carbon
Our materials need carbon. The challenge is to avoid releasing this carbon in the atmosphere by making it circular. In that way, we prevent the use of additional fossil resources.
Reference: https://renewable-carbon.eu/
Becoming circular
We need more electricity, and in fact more green electricity. While this work is in progress, we also need to look at recycling technologies to lower carbon emissions along the value chain. Recycling reduces carbon emissions in the value chain by skipping the initial steps of the production. The shorter the loop is, the higher the emission savings are. This is the case of mechanical recycling for end-of-life products.
However, mechanical recycling cannot be used in all situations. That is where chemical recycling intervenes here as a complementary solution using large waste streams like mixed packaging waste and end-of-life tires.
Circularity will only be reached if all recycling technologies are combined and with the support of all stakeholders. We invite all customers and partners to join the Plastics Journey and to co-create solutions how plastics are made, used, and recycled in a more sustainable manner on #ourplasticsjourney.

Chemical recycling
Chemical recycling intervenes here as a complementary solution using large waste streams like mixed packaging waste and end-of-life tires. This solution contributes positively to carbon emissions reduction if the way back in the value chain with the pyrolysis process emits less CO2 than incineration.
Mechanical recycling
Recycling reduces carbon emissions in the value chain by skipping the initial steps of the production. The shorter the loop is, the higher the emission savings are. Indeed, it does not stack up scope 1 and 2 emissions at the different stages. This is the case of mechanical recycling for end-of-life products.
Resource and energy savings in the USE phase
With our products, we already help our customers to save energy and emissions through excellent insulating materials or lightweight construction. We help to save resources and reduce waste because our materials make products durable for a long life of service. Consequently, it also comes with the challenge to collect them and make them available for mechanical recycling.
Feedstock composition will evolve over time
To reach a fully circular economy, all recycling technologies must be considered as they are complementary.
However, even if maximum recycling rates will be achieved, there will be a certain loss of material that should preferably replaced either by biobased carbon feedstock or should come from Carbon Capture and Utilization.
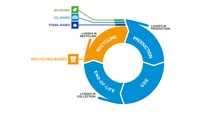
The future distribution of feedstock is to co-create
The distribution of fossil and circular feedstock is in constant evolution and a cooperative approach will accelerate the transition towards an optimized composition. Recycling will be the preferred solution, but fossil-based feedstock will probably be part of it as well.
Losses are part of the challenge
Even if maximum recycling rates will be achieved, there will be a certain loss of material along the value chain: in production, in collection, or in the recycling phase.
Reference: https://renewable-carbon.eu/
It is not clear today how the distribution of different feedstocks will look like. So we call all stakeholders to join us and co-create it, together.