Footwear
The shoe of the future has a cyber so(u)le!
"Cyber and 3D" is the theme around which the 27 young students who participated in the 16th edition of the "Footwear Design Contest" challenged themselves. Like all the competitions before, the 2022's edition also was organized by the school of footwear design and technology Politecnico Calzaturiero of Padua in collaboration with BASF Italia.
THE CYBER SO(U)LE & THE IDEA BEHIND IT
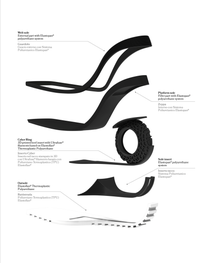
When human creativity meets footwear manufacturing of the future!
Every year, the students have to design the upper part of a shoe which has to align with the sole. Just as the years before, the sole is manufactured with BASF's materials and the base of the whole project - because everyone has to work with it.
Roberto Guzzonato is the designer of this sole, and an affirmed stylist in Europe and Asia. Thanks to a long academic and professional career, he stands out in terms of technical as well as creative aspects. Today, the firm "ROBERTO GUZZONATO snc" consists of a group of young energetic people with whom the Cyber 3D project was shared.
But where does the idea for a cyber competition came from? Roberto says:
The research and study behind this project led us to reflect on how quickly the world’s society has changed over the past four years, also due to the pandemic. Social relationships, Smart Working, video conferences, online shopping and everything concerning our daily life now relies increasingly on “social networks”.
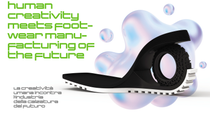
This thought gave rise to the desire to make this footwear Cyber and 3D. Cyber because it is the interaction between man and computers in reference to virtual reality and the internet, while 3D represents the three dimensions of space in a two-dimensional space.
The evolution of this project led to the creation of an elegant and lightweight sole defined of multiple elements that stand out for their innovative and original line projected towards the near future... the “METAVERSO”.
THE MATERIALS & MANUFACTURING PROCESS
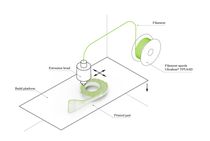
As for the materials, the full potential of the polyurethane family was exploited. For the welt and platform sole as well as the sole insert Elastopan® (PU) was selected. This is how comfort is provided, but without limiting aesthetic values. Elastollan® (TPU) fits perfectly for the outsole, because it ensures design freedom and performance simultaneously. The clearly visible cyber ring funtions as a stylish heel insert. It was 3D printed by using Ultrafuse® TPU 64D from Forward AM, a subsidiary of BASF. This material combines the best of two spheres by being a strong , yet flexible filament for fused filament fabrication.
As for the production of the sole, the decision was made for two processes: Well-established casting and injection molding as well as latest 3D printing technology in one ensemble – displaying the complete range of directions for footwear manufacturing from highest productivity and automation to utmost flexibility and individualization.
The successive creation of the molds was done by Off. Mecc. Giaquinto Ennio W. and C. s.r.l.. The production of the outsole, PU components as well as the final assembly together with the 3D printed Cyber Ring were carried out by Suolificio Negro s.r.l. – Vibram S.p.A.
THE WINNING DESIGNS
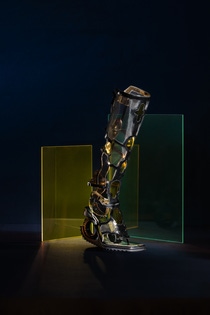
1st winner:
Silvia Toffanin
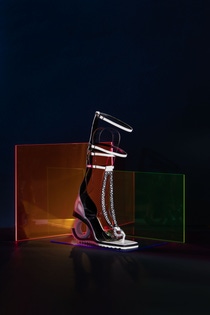
2nd winner:
Alessandro Corelli
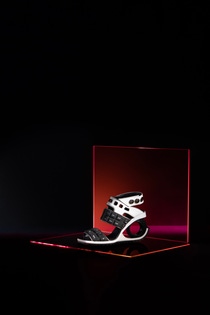