We are on our way
Plastics & Rubber
The transformation task: shifting away from fossil resources
Our society is facing one of the biggest economic, ecologic, and technical transformations in modern times. Fossil resources are limited. It is high time we shifted towards the use of environmentally friendlier alternatives. With this in mind we also need to rethink how plastics are made, used, and recycled, with the ultimate goal of a net zero circular economy that saves fossil resources and energy. If carbon is kept in production cycles and production is designed to generate as few emissions as possible, the circular economy is the key to achieving the net zero target.
How to move towards a circular economy with net zero emissions
The ultimate goal is a circular economy in which fossil resources and energy are saved wherever possible and the release of emissions is kept to a minimum.
At BASF, we are already working on various ways to make most of plastics during their use phase and at the end of their lifecycle and create new valuable resources from plastic waste by recycling. But the transformation efforts reach another scale when it comes to the sustainable making of our plastics, as it remains energy-intensive and is still associated with high CO2 emissions. At the same time, our plastics are a prerequisite for many value chains across almost all industries. Plastics will continue to play a major role in modern society in the future. The solution must be to manufacture them with as little environmental impact as possible.
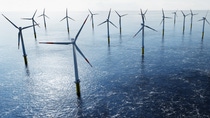
How to reduce emissions in plastics production
We massively want to reduce our carbon footprint along the value chain. Accordingly, we pursue different approaches on our way to net zero.
One central component of reducing greenhouse gas emissions is gradually shifting our energy supply to renewable sources. This applies to both our electricity and steam supply and our production processes, where we will increasingly replace fossil fuels with energy from renewable sources. The electrification of our processes will significantly increase the BASF Group’s green power demand over the coming years. In 2022, renewables accounted for 16 percent of BASF’s global power demand. We invest in our own energy production plants and enter contracts to ensure a direct supply of our sites with renewable energy with our make and buy strategy. By 2030, our projection is that this figure will rise to more than 60 percent. We believe that improving our own production processes and thus scaling up new technologies, like the electrification of our steam cracker will bring us a big step closer to reaching our net zero targets. And we have many more ideas.
Circular alternatives - recycled or renewable materials
We focus on feeding in alternative feedstocks instead of fossil feedstocks at the very beginning of a production process: These circular alternatives are recycled or renewable materials.
One way to account for this substitution is the mass balance approach. The amount of alternative feedstock fed into a multistep and multi-output chemical production process is attributed to a specific product in a way that customers can be sure they support the substitution of fossil resources with this product.
By using recycled feedstock, we reduce the volumes of plastic waste which are landfilled or incinerated. Chemical recycling saves CO2 emissions compared to incineration. The resulting products come with a smaller product carbon footprint. And our customers profit from the virgin quality of the mass balanced products.
Click here for more information on our way to climate neutrality in production beyond plastics: Carbon Management
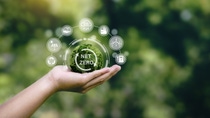
By using green power, low-carbon steam, renewable feedstocks, and highly efficient processes – we will be able to offer products with a distinctly lower carbon footprint and, ultimately, aim towards net zero products. In this regard, we are a pacemaker for other industries to rethink their processes towards a net zero circular economy, too.