Performance Polymers
Creating a closed-loop economy
BASF’s Nypel RC grades offer a sustainable solution
New generations of car buyers are more than ever aware of climate change and waste. They demand automotive products that contain more sustainable materials, just like they demand it from the consumer electronics and apparel markets.
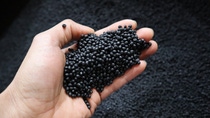
They also want to see evidence that OEMs are producing their products in as sustainable a manner as possible. Finding ways to produce products that build towards a closed-loop economy is a big part of that push, and BASF’s new Nypel RC grades are a part of that solution. Nypel also enables OEMs to meet upcoming global regulations for sustainable material use in transportation.
Nypel RC grades are an expansion of the BASF Engineering Plastics portfolio. They contain post-consumer recycled (PCR) and/or post-industrial recycled (PIR) material. Nypel RC grades can be formulated to contain virgin resins, additives, and fillers to support customers and applications in North America desiring recycled content.
How it’s made
One major sustainability benefit that Nypel offers is that it helps reduce landfill waste by utilizing an otherwise often discarded product: carpet.
The process of creating Nypel begins when used carpet is placed on a curb, sent to collection site, or gathered by new carpet installers. The polyamide polymer comes from the recycled carpet tuft that is separated from the other carpet components producing a carpet “fluff.” Additional processing occurs to further remove impurities present in the polyamide fluff. That polyamide can then be pelletized or densified.
The mechanically recycled Nypel polyamide products will continue to serve as a steppingstone toward a truly sustainable future
The PCR polyamide is supplied to compounders for use in engineering plastics. PCR used by BASF is sourced and tested for compliance with BASF quality standards and is utilized in the production of BASF Nypel product formulations that meet automotive OEMs’ specifications. General PCR contents include: PA6 or PA66; polymer and various byproducts of carpet production. The exact content levels depend upon carpet blends (commercial or residential carpet) and its recycling methods.
In addition to carpet, BASF is researching other products that could be used in the process.
“While the used carpet is our primary source of recycled polyamides, our research and development teams work on the continuous assessment of alternative sources, such as fishing nets, automotive airbag fibers, conveyor belts and more. Mechanically recycled polyamides have some limitations when it comes to performance compared to prime polymers. The cleanliness of the recycled stream is very important, especially for tough applications in powertrain components,” explains BASF’s Lenar Abbasov, Market Segment Manager, Transportation, Powertrain & Thermal Systems.
Transportation OEM solutions
OEMs in the transportation sector are constantly looking for ways to reduce their CO2 footprints as well as find longer-term end-of-life solutions that can reintroduce waste feeds back into a truly closed-loop economy.
“We're able to offer a polyamide product that has a lower product carbon footprint for the use in the components of internal combustion engines; therefore, making them a little bit cleaner and more sustainable,” Abbasov says. “Taking used carpet from the landfill helps to clean the environment as well.”
“As truly continuous loop Chemical Recycling technology – including BASF ChemCycling® – and the biomass balance (BMB) approach continue to grow and gain market acceptance, the mechanically recycled Nypel polyamide products will continue to serve as a steppingstone toward a truly sustainable future,” explains BASF’s Chris Korson, Transportation Sustainability Champion.
Transportation OEMs such as Ford, GM, Stellantis and other manufacturers are driving the push towards closed-loop economies.
“Transportation OEMs make this one of their top strategic priorities as well,” says Abbasov. “We help our customers to materialize these strategies by developing new recycled solutions.”
We're able to offer a polyamide product that has a lower product carbon footprint for the use in the components of internal combustion engines; therefore, making them a little bit cleaner and more sustainable.
Sustainability
Abbasov says there are significant sustainability benefits of using Nypel compared to the use of prime polymeric products.
“We’re able to reduce the amount of CO2 that's required to make the product because now we're not driving it to a reactor with the amount of energy that it takes to create a prime product. We are also making sure that certain waste is not introduced into a landfill, and that it's actually getting a second life and pushed back into the economy,” he says.
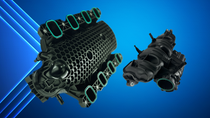
Good examples of Nypel applications in the transportation Powertrain segment are the air intake manifolds, which are vital components of the internal combustion engine’s air induction system.
“These components are produced by an injection molding process using PA6 compounds. For example, the Ford’s 7.3L engine air intake manifold is a massive part that weighs 17 lb.,” Abbasov says. “It is produced using Nypel RC6030F, a product that contains 25% of PA6 that comes from PCR carpet stream. The technical requirements for air intake manifolds are very challenging, and BASF has developed this product specifically to meet burst pressure targets. We now are ready to introduce a 100% PCR PA6 product that offers nearly the same burst pressure resistance as our partially recycled grades. It is a result of our continuous work with various PCR streams and new approaches in formulations for Nypel.”
It’s important to note that Nypel is a complimentary part of BASF’s overall portfolio for sustainability. While product lines like Nypel will continue to be a large part of the sustainability portfolio for several years, Abbasov notes that as the demand for sustainable materials continues to grow, he expects some of the other product lines to grow as well.
“In addition to mechanically recycled plastics, we already offer, and continue developing, our capabilities to offer more bio-based, biomass balance, and chemically mass-balanced products, that offer true closed loop solutions,” he says. “For us, Nypel is the first step in offering sustainable solutions. We are preparing for the true circular economy of the future.”
To learn more about Nypel, click here.