Automotive
Foaming simulation of PU systems now also available for car steering wheels
- Virtual process design improves air ventilation in molds and predicts foam density distribution
- Advantages for steering wheel manufacturers: faster component development and tailored, more reliable process
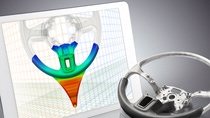
Under the virtual magnifying glass
BASF has expanded its simulation tool Ultrasim® so that it can now precisely predict the foaming and curing of the flexible integral foam system Elastofoam® I for car steering wheels. With the detailed simulation, the most important chemical reactions as well as the flow behavior of the polyurethane foam in the mold can be calculated. At every point in the mold, the simulation accounts for process and environmental conditions such as temperature, pressure and material concentration as well as special component elements such as the metal skeleton and cables. Based on the detailed description of the integral foam systems now available for the first time in Ultrasim®, it is possible to identify – like looking through a virtual magnifying glass – critical air voids in the component, to adapt air vents and to design a stable manufacturing process for steering wheels long before the mold is built. The new BASF service allows steering wheel manufacturers to reduce development cycles, thereby lowering costs, while at the same time realizing the trends towards greater functional integration, more electronics and individual design in steering wheels. It is used by automotive suppliers such as ZF-TRW Automotive Safety Systems
Despite complex flow behavior: Air vents and density distribution precisely predicted
Steering wheels are the most important contact points in a car: feel, look and functionality are linked directly to the component design. They are complex components whose shape and elements – including a metal skeleton, cables, buttons and design features – combined with limited space, make high demands on the polyurethane foam and the foaming process. The simulation is therefore based on extensive material data and complex material laws because all these aspects affect the filling behavior and the resulting density distribution. The flow behavior has to be modeled more precisely than in the case of e.g. instrument panels: the flow channels split up and rejoin, small slots have to be passed and thick areas have to be reliably filled.
A particularly critical parameter is the ventilation of the mold and the different methods used to implement it in the production process. The placing of air vents is intended to prevent air voids in the component as they impaire the stability and look of the steering wheel. The filling simulation with Ultrasim® can accurately predict the position and size of possible air voids and support customers to position air vents correctly: Thus the number of air vents as well as the risk of air voids can be reduced. The exact flow model also includes part and customer specific processes, e.g. the mold pivoting during the foaming process. Also in these cases, the prediction accuracy of the BASF simulation tool regarding flow behavior and air voids has been validated by comparison to manufactured customer components.
BASF’s simulation tool also calculates the density distribution. This is crucial for the feel, i.e. the local hardness of the steering wheel, which is prescribed by the car manufacturers. In order to predict the density at all points of the component, the material model for Elastofoam® I was further developed in such a way that it describes in detail the foam expansion depending on the chemical reactions, the local temperature development, the pressure and the initial gas concentration. This is the starting point for describing steering wheels made of polyurethane foam not only in terms of processing, but also for determining the mechanical behavior of the component itself, e.g. stiffness and hardness. Up to now it has been possible to measure the so-called shore hardness of steering wheels only in tests on the real component, but not to predict it in the earlier, purely virtual project phase.
Flexible integral foam Elastofoam® I: light foam core, firm skin
In addition to its established technical customer service, BASF is further developing the tailored-to-process-and-part manufacturing of its proven flexible integral foam systems with its new Ultrasim® service. In a one-shot process and combined with an in-mold coating the low-density Elastofoam® I forms an integral skin as a decorative and protective surface that is UV-, scratch- and abrasion-resistant. Steering wheels made of Elastofoam® I have a soft, comfortabel touch combined with a tough outer skin. They are wear resistant and durable, unaffected by sweat, sun screen or cleaning agents. Depending on the part geometry, current systems offer a significant weight reduction of up to 10 percent without loss of properties at demolding times down to 60 seconds and low emissions.