Automotive
Innovative plastics for design and comfort in the automotive interior
Parallel to the implementation of automated driving and accompanied by the emergence of alternative eMobility powertrain setups, the car interior will transform into an extended living room. With BASF’s Polyurethanes like Elastoflex®, Elastofoam®, Elastollan®, Elastocoat® and Elastoskin® as well as the Engineering Plastics Ultramid®, Ultradur® and Ultraform® modern and innovative automotive interior designs can be realized. Besides high-class surfaces, smart haptics, improved acoustics and long service life, the materials convince with efficient production, global availability accompanied by a reliable service. Cellasto® improves the noise, vibration and harshness performance of the vehicle and brings the automotive comfort to the next level.
Automotive interior in action
Here you can find customer stories, case studies and all the latest updates from our interior blog!
Latest Article from the automotive interior blog
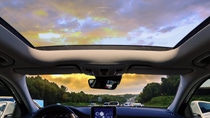
ChemcyclingTM Headliner
» Applications
Versatile applications for the automotive interior
Whatever your specific needs for your interior application: BASF connects new material developments with unique services in order to create system solutions which give your interior application the distinctive advantage.
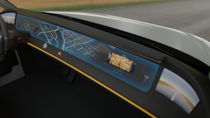
Instrument and door panel
Instrument panels are safety-relevant parts with extreme requirements. The foam has to fulfill high durability even in humid and hot environments. Elastoflex® E is well-suited for this purpose. The current portfolio for closed- and open-mold technologies offers low density solutions down to 100 g/l and fast demolding times down to 70s. Foaming in gaps smaller than 5 mm can be realized. Emissions are extremely low fulfilling VDA278 and chamber test requirements. Special soft grades are available fulfilling harsh heat and humid aging tests requested by OEMs.
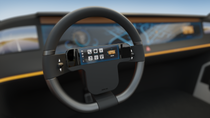
Steering wheel
Steering wheels made of the flexible integral foam Elastofoam® I have a soft, comfortable touch combined with a tough outer skin. They are wear-resistant and durable, unaffected by sweat, sun cream or cleaning agents. State-of-the-art low emission systems offer a significant weight reduction down to 340g/l without loss of properties at demolding times down to 60 seconds.
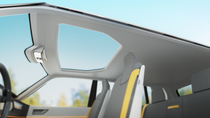
Headliner
Car headliners are the biggest surface to absorb sound and reduce vibrations, though available space is limited. BASF thermoformable foam systems Elastoflex® E 3943 perfectly fit to this application. The low density foam systems down to 22 g/L offer outstanding acoustic properties while providing high stiffness and very low emissions. The ISO 116 product line complements the portfolio by lamination adhesives for high productivity and low scrap rate.

Trunk floor
Elastoflex® E 3532 is the ideal resin to realize extremely lightweight honeycomb-sandwich structures due to easy and fast processing. No matter which part size, usage of our thermo-activated systems ensures thorough wetting of the fibers, a firm bond with the sandwich core and rapid curing. Due to its excellent mold-release properties, tailored rheological profile and low temperature curing mechanism, a resource-saving efficiency in the whole production process is given.
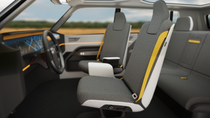
Seating
BASF provides fully formulated Elastoflex® W systems or special isocyanate solutions for comfortable seats with high productivity even at low densities down to 40g/l. Foam hardness is directly adjustable on the application machines in a wide range. Different hardness zones in a seat allow a combination of strong seating support with a soft feel for increased comfort. Elastoflex® W foam systems are extremely durable under dynamic loads for long service life.
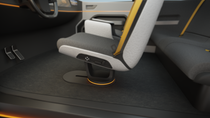
Acoustic foam
Acoustic comfort is a key contribution to the passenger’s wellbeing in a car. Elastoflex® W flexible foams allow car designers to tailor the acoustic perception of the car interior. Tailored acoustic properties, low densities, good processing behavior and low emissions are key requisites for state-of-the-art carpet back-foaming and related applications.
Detailed material information for car interior solutions
» Polyurethanes
Our versatile PU systems for the automotive interior
With their versatile properties and unlimited application possibilities, our PU systems can make the automotive interior safer, more comfortable and more beautiful. BASF polyurethanes can be adjusted to many different densities, they can be soft or hard, flexible or stiff, they resist hot and cold temperatures as well as many aggressive media.
» Engineering Plastics
Engineering Plastics
Emission-optimized instrument panels, acoustically effective roof linings or solid, high-quality surfaces – Engineering Plastics by BASF offer versatile application possibilities for less weight, optimum comfort and low emissions. BASF materials for the automotive interior ensure the following features:
- Great design freedom
- Detailed representation
- Excellent haptics and look
- Optimum combination of strength and stiffness for structural parts