Automotive
Fossil resource substitution in the automotive industry
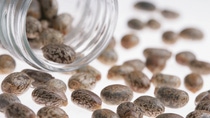
Bio-based solutions with castor oil
Automobile manufacturers and processors are always searching for new, cost-effective solutions for more efficient components. This imposes a variety of challenges on material suppliers. For example, highly complex instrument panels must comply with current requirements while at the same time supporting trends like autonomous driving. The complexity of this safety component is increased both by the size, design and safety requirements and by the possible incorporation of technical equipment. On top of that, the dashboard must also provide the driver with the maximum comfort and feel pleasant to use.
BASF has been supplying advanced PU foams for foam-backed instrument panels for many years. The production process involves injecting a polyurethane foam between the outer skin and the support of the instrument panel, bonding the surface and support material together. The foam produces a material that has a very soft haptic. These customized systems are attractive because of their low emissions and offer optimum adhesion to surfaces produced from a wide range of materials. Even PVC skins can be processed easily.
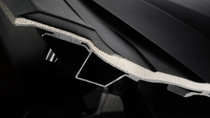
As part of this new generation of systems, BASF has also developed a foam system based on renewable raw materials. Elastoflex® E 3496/102 uses castor oil as a renewable raw material and can be used to produce complex components that are both light and thin with excellent adhesion to a wide range of surfaces. This successful development was awarded the SPE Environmental Category Award at the end of 2017. The project shared the prize for sustainable innovation with International Automotive Components (IAC).
This renewable product is available in Asia Pacific, North and South America.
Ultramid® S Balance
As the demand for bio-based raw materials is increasing worldwide, the introduction of Ultramid® S Balance for monofilament applications is another contribution of BASF to support this trend. The high performance polyamide 6.10, partly based on renewable resources, is available in various viscosities. The bio-based sebacic acid, which is used to produce Ultramid® S Balance, originates from the castor oil plant. In compounded and glass-fiber reinforced versions, BASF has already introduced the material in different commercial applications, e.g. in a design lamp or automotive quick connectors.
Polyamide 6.10 offers unique mechanical properties such as higher dimensional stability and softness compared to polyamide 6 or polyamide 6.6. Many of the benefits arise from less moisture absorption and higher carbon content. Due to its specific properties, Ultramid® S Balance can be used in various monofilament applications, e.g. filters for paper machine clothing or industrial brushes, as well as textile fibers and different engineering plastic applications.