- cutting-edge simulation framework for particle flow by coupling Computational Fluid Dynamics (CFD) with Discrete Element Method (DEM)
- simulation of filling behavior as a customer service
Performance Polymers
Ultrasim® for Infinergy®: Optimize processing and part performance
Ultrasim® is the versatile and flexible CAE competence for your innovations using Infinergy®. Our calculation of component concepts on a virtual basis starts with appropriate materials and adequate material models, ranging from the virtual prototype and ideal manufacturing process to the finished mass-produced component.
ULTRASIM® IS WHAT YOU NEED!
Why? Convince yourself:
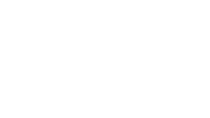
Ultrasim® offers a unique combination of CAE tools and material know-how. That opens up the possibility of predicting part performance - even before manufacturing the first prototype.
It creates a digital twin by taking into account variables that influence part performance. This way, it allows to optimize the part design and support you along the processing chain to achieve your goals.
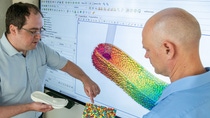
Do you need help?
Feel free to contact our experts!
Our experts are always happy to help you.
No matter what!
Click here to jump directly to the contact formular
How does the process for Infinergy® look like in detail?
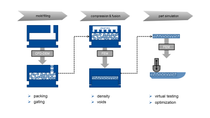
Have a look at every step in detail:
Possible Simulation Support for 3D Lattice Inserts
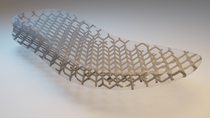
Filling Simulation
- mold filling with inserts possible
- prediction of density or void distribution
Part Simulation
- hybrid parts of Ultrasint® and Infinergy® can be simulated
- prediction and optimization of sole stiffness