Automotive
Lightweight and emission reduction - roof frames made with Ultradur High Speed
The new rheological modified Ultradur® High Speed has an outstanding flowability that is crucial to obtain large and slim interior trim parts. Moreover, considering its unprecedented processing advantages, we have been able to reduce weight without losing stiffness and dimensional stability at high temperatures.
The trend to panoramic roofs is ever increasing in the automotive industry. Car customers include panoramic roofs at the top of the list of extras when buying a new car. This trend coexists with the need to reduce the weight of all automotive components to minimize CO2 emissions. With the development of new Engineering Plastic parts for its interior applications, BASF and Grupo Antolin are complying with these challenges. The newly developed panorama roof is integrated into the ceiling trim (called the headliner) of the car which is made from the very light Polyurethane Elastoflex® E 3943/134. The actual sunroof opening in the headliner is supported by a structural bracket. Traditionally this is made of heavy steel. With Ultradur® High Speed a metal replacement solution is now used. Besides a high dimensional stability, the Engineering Plastic convinces with excellent mechanical properties.
In close cooperation, both companies have successfully validated the Polybutylenterephthalate (PBT) Ultradur® High Speed in plastic frames for open panorama headliners. The novel and newly design of these parts allow a weight reduction up to 60% compared to other traditional solutions. This special material allows the injection of large parts with unique performance such as excellent dimensional stability, low warpage at short cycle times, high stiffness, high temperature resistance and an outstanding flowability.
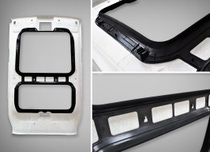
One of the main advantages of the newly designed plastic parts is the change in the process. We attach the frame to the headliner. During the production process the panorama reinforcement frame is fixed to the interior trim part while at the same time the part is formed in the mould. That leads to the elimination of additional process steps and moreover it improves tolerances during assembly and the quality of the final part is increasing. In addition, the new process does not involve the use of any solvents nor generate hazardous emissions.
Following the predevelopment with a German customer, the first pilot project was launched for a best-seller vehicle with outstanding results. More opportunities with this solution have been identified for several OEMs at global scale.