Performance Polymers
For your eMobility innovations: high performance material solutions
Let’s drive a truly sustainable future together
Your eMobility visions begin with BASF, the leading chemical supplier for the automotive industry. Our goal for your eMobility applications: Ensuring they meet the highest standards for safety, durability, and mechanical strength. Backed by decades of application development expertise, our high-performance materials meet the demanding conditions in the automotive industry. We provide you with the necessary tools and support to design trend-setting eMobility innovations – while also contributing to a sustainable future.

Don't just take our word for it, read what our customers and partners have to say.
Interested in discussing your next eMobility project with us?
Consult with one of our experts now.
Navigate through our eMobility applications
Interested in solutions for a specific application? Click on the appropriate field to learn more about our high-performance materials solutions.
Discover how our eMobility solutions make a difference
Looking for more details?
Keep being informed about our high-performance materials
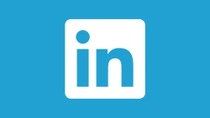
Find us on LinkedIn and check out the latest news, stories and event updates.