Construction
Wrapped up in the icy expanses – how the right insulation makes a polar station habitable
Thermal insulation is usually all about comfort and energy efficiency. In some places, however, it is also vital for survival – as on King George Island in the Antarctic where the temperature stays below zero even on “mild” days. This is why the BASF Elastopir® insulation material was chosen for the construction of a new research station.
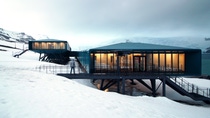
The Brazilian Comandante Ferraz research station is currently being built on the Keller peninsula near the tip of the Antarctic. The complex raised on stilts with its dark metal envelope hovers almost like a UFA in the endless white of the surrounding snowscape. The almost 5,000 square meter research station was successfully completed in January 2020. It consists of two main blocks – the upper one containing the living quarters of the 64-strong team, and the lower one 17 research laboratories and the service rooms. The client for the structure situated 600 km from the southern tip of South America is the Brazilian navy and the Ministry of Science and Technology. The competition launched in 2013 was won by architects Estudio 41 – who were faced with the task of creating a safe and comfortable working and living environment under the most testing climatic conditions. Pure functionalism, however, was not all, because the building’s aesthetics were considered important as well. It was also a question of minimizing the impact on the local environment with its flora and fauna. And it was nature that made the design and construction so challenging. The station’s façade has to withstand extreme sub-zero temperatures as well as large quantities of snow and the often very strong winds. It also has to resist corrosion and keep maintenance needs to a minimum. Since its predecessor was destroyed by fire in 2012, the new station has to display optimized fire behavior in addition.
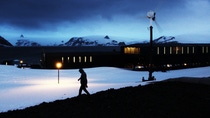
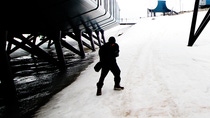
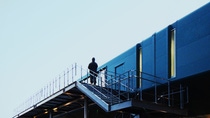
Outstanding under
Extreme Conditions
Insulation capable of delivering all this was found in a new generation of PU rigid foams from BASF. The decision went in favor of flame-retardant sandwich elements containing pentane-blown Elastopir® rigid foam – installed by BASF’s longstanding customer Jingxue Energy Saving Technology Co., Ltd. The company is China’s leading supplier of energy-efficient insulation systems and cold stores. Thanks to its extraordinary product characteristics – first and foremost, its low thermal conductivity and excellent mechanical strength and thermal stability – Elastopir® is equal to the challenges of the Antarctic in every respect. Furthermore, high fire protection standards can be achieved with the material in places where other insulation materials reach their limits, as the PIR structures formed with the aid of special PIR catalysts withstand temperatures up to 260 °C. On contact with naked flames, the PU rigid foam carbonizes and thus protects the structures behind it. Elastopir® systems based on polyisocyanurate (PIR) satisfy all key requirements of the most important fire tests.
Prepared for Anything
To keep construction time to a minimum under the adverse conditions on site, good preparation was essential for everyone concerned. All the insulation elements both for the external envelope of the Antarctic station and for special areas like the laboratories were prefabricated at Jingxue’s Chinese headquarters, supplied punctually by the fall 2018 and then installed rapidly on site on King George Island. The use of building modeling technology across all trades ensured that construction has been proceeding with precision and swiftly. This is particularly important, as mistakes here can cause huge delays. The replacement of damaged parts or the subsequent delivery of missing ones can even take weeks owing to the station’s isolated location. And even in the Antarctic summer, it is possible for blizzards to hold up work for days on end.
Varied Applications – Reliable Results
PIR solutions from BASF have already proven themselves at very low temperatures in previous applications. Such insulation elements are in use among other things in what is currently the world’s biggest indoor skiing center in Harbin, northern China. At a constant -5°C, up to 20 million visitors per year can pursue their passion for skiing. Yet the possible applications of Elastopir are varied: be it for production plants, warehouse buildings or cold stores in industrial construction, several hundred structures in China and other Asian countries have already been equipped with the system. And it is now all set to demonstrate its strengths in the Antarctic. So that research can be conducted in the warm and in comfort even at the southernmost corner of the world.
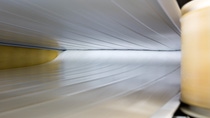
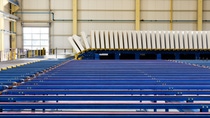
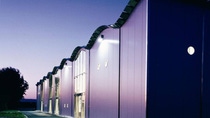
Elastopir has successfully withstood the test of time.
What challenges does Antarctica hold for construction projects - and how can we master them? That’s what we talked about with Jingxue Energy Saving Technology’s WU Siquan.
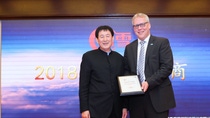
CORPUS: When Jingxue was approached about equipping the research station on King George Island – what were your first thoughts in terms of the project’s scale and possible challenges?
WU Siquan: We received news from the Chinese Ministry of Electronics Industry that the Brazilian military needed to rebuild the antarctic expedition station and required facade panels as part of that newbuild. At that time, there were two major challenges: First, the thickness of the sheets had to be 200mm plus to meet the insulation needs of the Antarctic region, which placed high demands on raw materials as well as manufacturing processes. Second, the materials had to be environmentally friendly, especially not causing any damage to the ozone layer.
CORPUS: Is the Comandante Ferraz antarctic Station like anything you have done before? Or was it a special project even for Jingxue?
WU Siquan: This is the first time we have worked on such a project.
CORPUS: Regarding the project’s scale – how long did it take Jingxue to produce and deliver all the panels for the station’s facade as well as for additional facilities like the laboratories?
WU Siquan: We had to deliver a total of 14,000 square meters of sheet metal. We spent almost six months preparing – this includes BASF’s material fomulation commissioning, mold and equipment retrofits. Production took close to 12 months.
CORPUS: How did you decide which insulation material to use in this very project? And why exactly did you go for BASF’s Elastopir?
WU Siquan: Apart from BASF, we also spoke to other international and domestic raw material suppliers. The main reason why we chose BASF in the end is that in the thermal insulation industry, BASF’s product application is mature by comparison, and there have been many successful cases globally. Elastopir has successfully withstood the test of time. In addition, BASF’s teams are experienced in working for global cooperations. This project finally found the right formula under the joint efforts of the Asia Pacific and European teams.