Electronics & Electric
Elastopor®(PU) : Intelligent sandwich technology for efficient insulation, cooling, storage and transportation
Versatile and with low thermal conductivity, Elastopor® is a closed-cell polyurethane rigid foam that makes energy-efficient construction possible.
Important Notice
On 21.03.2023, BASF SE and Systemhouse s.p.r.l. have agreed to settle their pending lawsuit in which BASF claimed infringement of its patent protected adhesion primer technology for PIR sandwich panels protected by European Patent EP 1 516 720 B1. Systemhouse s.p.r.l. has taken a license for the asserted patent familiy and respects BASF's Intellectual Property.
The use of sandwich panels and insulation boards made of Elastopor® and Elastopir® in sandwich technology means an optimum combination of excellent mechanical and physical properties and thermal insulation. Elastopor® is used as the core material of multi-layer construction elements and is used with a diffusion-tight metal cover layer for wall, floor and roof elements in industrial hall, refrigeration and warehouse construction. The metal composite elements are manufactured in continuous (double belt) and discontinuous (press) production. In residential construction, insulating elements with flexible cover layers such as aluminium foil or mineral fleece and a core of Elastopor® are also used. The main areas of application here are pitched and flat roof insulation as well as exterior wall and floor insulation. Elastopor® rigid foam systems are easy to process and guarantee high product quality. The polyurethane insulation products with different laminations and functional layers are an advantage for producers and consumers. As energy-efficient insulation they are an active contribution to climate protection.
Check out our latest stories
Go!Create Polyurethane insulated panels for refrigerated truck bodies
Watch our inspiring customer success story from South Africa, the result of collaboration between the BASF Performance Materials team and GRW in South Africa. A journey towards creating global industry standard polyurethane insulated panels for refrigerated truck bodies. Hear from some of the dedicated individuals who combined their expertise to make it possible.
Key Properties of Elastopor®
- Excellent mechanical properties
- High insulation effect even with low material thicknesses
- Very good bonding with different facing materials
- Prefabricated panels with Elastopor® permit rapid and straightforward installation
- Durable and low-emission
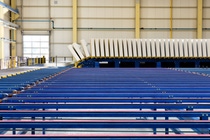
Elastopor® Application Range
The applications are as manifold as its product properties: Explore the various application possibilities of Elastopor®!
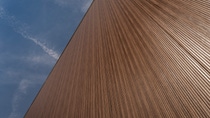
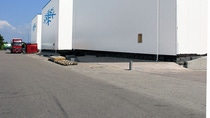

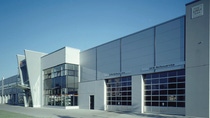
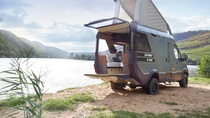
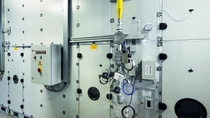
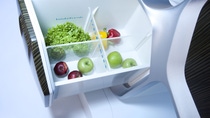
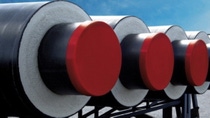
Better Technology – Better Foam
Many components are crucial for superlative quality in the production of polyurethane sandwich elements. Along with our precision-tuned polyurethane systems BASF also offers solutions in state-of-the art process technologies. The patented rake technology of BASF makes the production of polyurethane sandwich panels more stable and more cost-effective. With its modular design, the patented rake replaces conventional laydown devices and can be adapted precisely to the construction panel being produced.
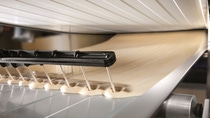
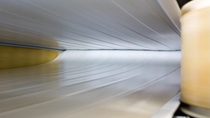
Elastopor® is able to flow through and adhere to complex shapes and surfaces which provides a freedom of design as well as complete insulation, even in unconventional designs.
Tailor-made Solutions
Tailor-made for individual needs: We support our customers in developing application-oriented solutions.