Performance Polymers
Elastolit® D/R/K - systemy pianki sztywnej integralnej i RIM
Elastolit® D i Elastolit® K są systemami pianki sztywnej integralnej i kompaktowych duroplastów produkowanych przez BASF. Wyróżniając się licznymi właściwościami, stanowią doskonałą, opłacalną alternatywę dla klasycznych materiałów budowlanych takich jak drewno i metale lub materiały termoutwardzalne i techniczne tworzywa termoplastyczne.
Dzięki szerokiemu zakresowi właściwości pianki Elastolit D i Elastolit K znajdują zastosowanie na wielu obszarach, takich jak produkcja drzwi wewnętrznych i zewnętrznych oraz elementów wystroju wnętrz, skomplikowanych mebli, wyposażenia wewnętrznego samochodów, nart, desek snowboardowych i części eksploatacyjnych.
Elastolit® D (systemy sztywnej pianki integralnej)
Dzięki przekładkowej konstrukcji (szczelne poszycie i mikroporowaty rdzeń) Elastolit D idealnie nadaje się do formowej produkcji części o wysokiej jakości, charakteryzujących się dużą sztywnością i małą masą. Ponieważ w formie stosowane jest tylko niskie ciśnienie, można w ekonomiczny sposób produkować elementy wielkogabarytowe. Możliwe jest też integralne osadzanie wzmocnień i elementów przenoszących siły.
W podobny sposób z wielką precyzją można produkować złożone, przestrzenne elementy o długich drogach przepływu i cienkich przekrojach. Oprócz tego Elastolit uzyskuje dobre parametry, gdy chodzi o izolację termiczną i akustyczną. Na zamówienie Elastolit D może być dostarczony w odmianie łatwo wyjmowalnej z formy i ognioodpornej, spełniającej wymagania różnych norm (UL 94, DIN 5510).
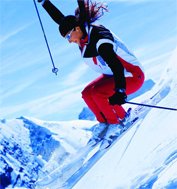
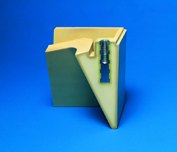
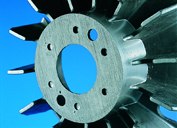
Elastolit® K (Systemy kompaktowej sztywnej pianki integralnej)
Elastolit K jest materiałem mikrokomórkowym, niemal litym, charakteryzującym się niskimi kosztami przetwarzania. Nadaje się do produkcji części wielkogabarytowych o długich drogach przepływu i ściankach o preferowanej grubości od 3 do 6 mm, cechujących się wysoką naturalną sztywnością i dobrą wytrzymałością. Wiskoelastyczne właściwości Elastolitu K sprawiają, że można z niego wytwarzać elementy z drobnymi detalami geometrycznymi, podobnie jak z tworzyw termoplastycznych, a w uformowanych częściach mogą być od razu osadzone łączniki zatrzaskowe.
Materiał ten jest też atrakcyjny przy produkcji średnioseryjnej, gdyż umożliwia stosowanie tanich form aluminiowych i ma krótki czas cyklu produkcyjnego. Na zamówienie Elastolit K może być dostarczony w odmianie łatwo wyjmowalnej z formy i ognioodpornej, spełniającej wymagania różnych norm (UL 94, DIN
Elastolit® R (systemy RIM)
Szczególną cechą Elastolitu® R - materiału również mikrokomórkowego, niemal litego - jest wysoka udarność, nawet w bardzo niskich temperaturach. Sztywność formowanych części można dodatkowo zwiększyć, wprowadzają do nich zbrojenie z włókna szklanego lub mineralnego. Gotowe części są stosowane głównie w branży motoryzacyjnej, jako elementy nadwozia samochodów osobowych (przedni i tylny dolny fartuch, nakładki na progi) i użytkowych (wielkogabarytowe panele nadwozia, błotniki itd.). Grubość ścianek części gotowych generalnie wynosi od 3 do 4 mm, a czas wyjęcia z formy mieści się w granicach 30 do 180 sekund. Zastosowanie nowo opracowanych systemów pozwala produkować elementy nadwozia o dobrej naturalnej sztywności i ściankach grubych zaledwie na 2 mm, przy czasie wyjęcia z formy wynoszącym 30 sekund (technologia elementów
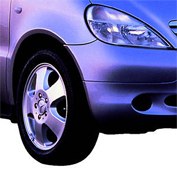
Nasz konsultant techniczny
Radosław Owerko +48 601 803 946
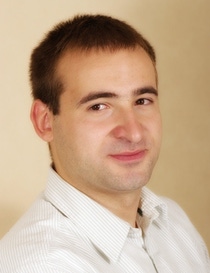