Performance Polymers
Go renewable With the World’s First Biomass-Balanced Polyethersulfone (PESU)
Challenge: Meeting Sustainability Goals with High-Performance Plastics
As all companies using plastics, firms that rely on high-performance thermoplastics are also facing the task to reduce their emissions. Their challenge of achieving their sustainability goals lies mainly in using sustainable materials without compromising on material performance, quality, or requiring additional investment in new processing lines. Maintaining this delicate balance is especially important for industries such as household/catering, automotive, and electrics and electronics (E&E), where high-performance plastics are essential.
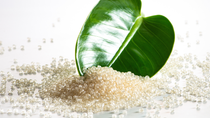
Solution: Introducing Ultrason® E 2010 BMB: A Biomass-Balanced PESU
In response to this challenge, BASF has introduced the world’s first biomass-balanced polyethersulfone (PESU), Ultrason® E 2010 BMB. In this groundbreaking material fossil feedstock is replaced with renewable alternatives derived from waste-based resources at the beginning of production. The renewable feedstock is attributed to the BMB grade through a certified biomass balance approach, ensuring that the sustainability benefits are transparent and verifiable. Ultrason® E 2010 BMB offers the same properties, performance, machine processability, and certifications as its standard Ultrason® counterpart, making it a seamless drop-in solution. This means that customers can achieve their sustainability goals without the need for re-qualification or adaptation of their existing manufacturing processes.
Results: Achieving Lower Emissions and Renewable Feedstock Use
Ultrason® E 2010 BMB supports industries as diverse as household, automotive, healthcare and water/sanitary in increasing the use of renewable feedstock and reducing emissions. The renewable feedstock used in Ultrason® E 2010 BMB comes from organic waste and is attributed to the product via a mass balance approach certified according to ISCC PLUS. This results in a lower product carbon footprint (PCF) compared to the standard BASF material, thanks to the use of renewable feedstock and 100% green electricity in the production process at BASF's Ludwigshafen plant in Germany. BASF provides transparency to its customers by offering PCF data to help them evaluate the PCF of their own products.
Join the Green Transformation with Ultrason® E 2010 BMB
Discover how Ultrason® E 2010 BMB can help your industry achieve its sustainability goals without compromising on performance or quality. Contact BASF today to learn more about this innovative solution and how it can benefit your products.