Performance Polymers
Making eMobility a Reality
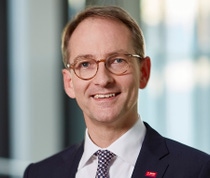
Author: Martin Jung, president of BASF’s Performance Materials
The widespread adoption of electric vehicles will have lasting effects on every segment of the automotive industry, from suppliers to consumers. For over 100 years, many suppliers designed parts specifically for engines, and now they must shift from tradition to design parts for batteries. A recent report by BloombergNEF found that in 2021, global passenger electric vehicle sales grew by 103 per cent to almost 6.6 million vehicles. While this eMobility evolution brings challenges, it also provides great opportunity for suppliers to create new business and change the transportation industry holistically to become more sustainable.
Transportation Transformation
The shift to electric powertrains and a greater emphasis on sustainability means automotive suppliers must take an all-encompassing approach to sustainable transportation. Tier suppliers, OEMs, and other players must work more closely than ever throughout the value chain to create solutions that meet changing performance requirements, ambitious CO2 fleet management goals, recycling targets, and regulations.
As a leading chemical supplier to the automotive industry, BASF is committed to working alongside suppliers and OEMs to create solutions that deliver on the promise of eMobility and a sustainable future. We create products for every part of the electric vehicle and for the charging infrastructure, while working to reduce our overall carbon footprint and therefore that of these vehicles.
With over 30 years of experience in sustainability work, BASF continues making strides to be ecofriendly throughout the supply chain and in our operations. We developed a biomass balance approach, replacing fossil resources with bio-based, renewable materials in the first stage of chemical production. This approach enables automakers to use more sustainable biomass and reduce emissions within their existing supply chain since the exchange of resources begins with our raw materials.
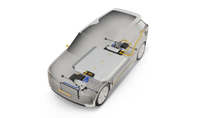
Shifting Priorities: Engine to Battery
Transitioning to eMobility will take time as suppliers convert their productions from internal combustion engines to electric vehicles and, in doing so, they are facing some strong headwinds including further developing the right talent, rising costs, and safety issues.
Suppliers producing plastic components for automotive applications need to help their talented materials engineers acquire the new knowledge necessary to develop materials specific to electric vehicles. For example, plastics engineers who used to design materials for combustion engines may now find themselves in the department for battery components.
Another dilemma impacting the whole automotive industry, from raw material producers to OEMs: the increased cost of raw materials, plus exploding energy and transport prices. For suppliers, this is especially problematic as there is no opportunity to pass on the increasing costs to OEMs because of long-term supply contracts. Due to that fact, some suppliers are already in a critical business situation. A close partnership of the whole industry is essential, otherwise Tiers will disappear from the market. That will impact the whole automotive supply chain.
This eMobility transition also comes with safety concerns that need specific considerations in the design phase. While electric vehicles carry a small risk of catching fire, lithium-ion batteries that power most EVs now in development are susceptible to heat and can ignite if they get too warm - unlike gas-powered vehicles that require a spark or flame to ignite. Preventing the battery from leaking is key in reducing the risk of battery fires. There are different ways to do this: innovative cooling concepts, high-temperature-resistant barrier materials, exhaust systems. Some automakers may use flame-retardant materials, but there are other technically constructive solutions to consider.
With a challenge this complex, collaboration will be the key to success. That is why BASF works in close partnership with our customers to tackle these issues together. We work with customers to develop and produce eMobility solutions specific to their individual needs. Suppliers with decades of experience in developing material solutions know that there is no one-size-fits-all solution to every problem. An innovation-oriented approach with strong R&D and open-mindedness will help drive eMobility forward.
The Key to Sustainable Mobility: eMobility + Renewable Energy
Modern vehicles must be built more efficiently and with a lower environmental impact, and with this transformation to electric powertrains, chemistry will play an even greater role in sustainable mobility. There are different demands on components due to new architecture and platforms for electric vehicles. OEMs are looking for new designs and material properties, and electrification is only one piece of the puzzle.
The other piece? Renewable energy and resources. At the start of the automotive value chain, suppliers source energy and materials used during production from renewable resources. Climate change is a major global challenge, and many automakers are targeting net zero CO2 emissions. To hit this target, the industry needs to become more efficient in automotive production and energy usage, increasing use of renewable energies and accelerating the development of new CO2-free processes to produce chemicals.
The key to achieving clean, green mobility goes beyond suppliers simply designing environmentally-friendly solutions. As an industry, the focus needs to be on ensuring that every step of the value chain is sourced responsibly. To achieve this, suppliers must encourage circular economy initiatives that go beyond the conventional take-make-dispose approach. Creating entirely new business models allows automakers to separate growth from raw material consumption and to use resources in the most environmentally-friendly way across the entire value chain.
Drive Forward – Together
The success of this transformation requires the entire industry to work together. Catena-X, for example, is a network comprised of automotive manufacturers and suppliers, dealer associations, and equipment suppliers. Its goal is to create a uniform standard for information and data-sharing along the automotive value chain.
As the automotive world puts more emphasis on eMobility being the future of transportation, suppliers, OEMs, and other industry partners must continue investing in the technology, talent, and expertise to ensure electric vehicles will indeed result in a sustainable future for all.