Plastics & Rubber
The importance of recycling:
Unlocking potential through complementary recycling technologies
Around 350 million tons of plastic waste is generated every year, but only about 10 percent is recycled. One reason is that there is no "one-size-fits-all" solution.
A variety of recycling approaches is needed to achieve circularity
In the coming years, sustainable practices and waste management will increasingly depend on a variety of recycling technologies. Rather then competing, these technologies will work together to enhance efficiency. As mechanical recycling methods reach their limits for some waste streams, the importance of chemical recycling routes will grow ensuring no opportunity for circularity is left untapped. This is why BASF supports all types of recycling technologies.
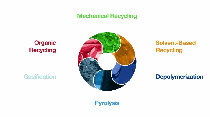
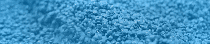
To accelerate #ourplasticsjourney, we are working with partners along the value chain on several projects of different maturity levels. We offer solutions that further improve mechanical recycling and use new, innovative and complementary chemical recycling technologies on a large scale.
Watch the videos below to find out how!
Plastics circularity requires a variety of solutions to address the broad range of applications and their resulting end-of-life materials. Chemical recycling technologies are suited for waste streams for which mechanical recycling is not applicable, for example mechanical recycling rejects or end-of-life tires. BASF has established partnerships with technology companies Quantafuel, Arcus and Pyrum which supply us with pyrolysis oil. We feed the oil as recycled feedstock into our integrated production network and attribute it to certified Ccycled® products through a mass balance approach. BASF customers have successfully introduced Ccycled® products in various industries like (food) packaging, textile and automotive.
ARCUS is a greentech start-up company founded in 2016. By means of its technology, it aims to use its technology to sustainably recycle plastic waste that cannot or only with difficulty be recycled in the carbon cycle and thus to use fewer fossil raw materials on the one hand and to master the global challenge of plastic waste on the other. ARCUS Greencycling Technologies GmbH is based in Ludwigsburg.
More information about BASF's ChemCycling®.
BASF has developed a wet chemical recycling process for used mattresses made of flexible polyurethane. Initial small-scale trials have been very promising. The original polyols can be recovered from the used mattress foams and used again to produce high-quality flexible foam blocks. The quality of these flexible foam blocks made from recycled polyurethane are equivalent to those made from conventional materials from fossil raw material sources. Thus, high-quality new mattresses can be produced from alternative polyurethane.
BASF offers a range of innovative solutions for mechanical plastics recycling from waste sorting to washing to improve the mechanical recycling process and to enhancing the quality of recycled polymeric materials with additives. We leverage the expertise of our partners like Sirmax to accelerate our journey towards a circular economy for plastics. Sirmax Group, headquartered in Cittadella, Italy) is a leading independent European producer of polymer compounds used in all sectors: Automotive, Household Appliances, Power Tools, Electrical & Electronics, Construction and Furniture. In 2019, Sirmax acquired 100% of SER in Salsomaggiore Terme, specialized in the recycling of plastics. This acquisition is the first step of a larger project aimed at becoming an important global player in the circular economy business in the main market segments.
We are recycling end-of-life textiles at a molecular level ready to be transformed into brand new, premium fabrics. loopamid® is the recycled polyamide 6 based entirely on textile waste. This is true recycling, the first step to a circular economy for textiles. By reprocessing old textiles into new fibers, yarns, fabrics, garments and garment accessories, we reduce the demand for virgin materials and mitigate the environmental burden of waste.
More information about loopamid®.
Find loopamid® on LinkedIn.
More information about loopamid®.
Find loopamid® on LinkedIn.
More projects to follow. Stay tuned.