Automotive
Two polyurethane families for esthetic and haptic requirements
Highlights in car interiors
Chemists at BASF Polyurethanes GmbH have paved the way for elegant car interiors by developing two tailor-made polyurethane (PU) solutions, namely, Elastoskin®, the in-mold-coating (IMC) spray skin, and Elastollan®, the hard-phase-modified aliphatic thermoplastic polyurethane (HPM-TPU). Both surface materials stand out for their luxurious look and exquisite feel. The IMC spray skin, an aromatic PU system, is relatively soft since it is also back-foamed. This is why it is employed whenever good haptic properties in response to pressure are valued in areas such as instrument panels, armrests or inside door paneling. HPM-TPU, in contrast, yields a soft touch (tactile sensation). Parts with Elastollan surfaces are not back-foamed. Moreover, the lightfast TPU does away with the otherwise necessary laborious off-line coating process. Application examples are door handles, center console covers and cup holders.
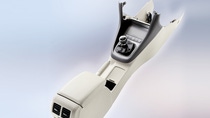
New generation of spray skin with potential in lightweight construction
The new generation of Elastoskin spray skin weighs up to 20 percent less than the standard product introduced three years ago. This weight reduction is achieved by physically expanding the PU system with air. The machine manufacturers Hennecke and KraussMaffei have developed special mixing heads for this particular purpose. The new skins not only contribute to lightweight construction but they are also less expensive thanks to the savings in material. As was the case with the older variant, the new spray skin is applied into the open mold and affords a great deal of design freedom in terms of color and surface texture. Its surface can hardly be distinguished from leather and its pressure behavior meets the strictest standards of the automotive industry. Among the many different kinds of plastic system solutions for instrument panels, the IMC offers highest performance.
Making its way into the luxury class
Thanks to its upscale look, this material has entered the interiors of high-end automobiles. For some years now, the inside door paneling in Daimler’s S and SLK classes have had an Elastoskin surface that surrounds the car’s occupants in high comfort. In September of 2009, BMW started using IMC spray skin for the instrument panel of its 5 GT, and other models and components will follow.
A good example demonstrating that Elastoskin is already today on the cutting edge of the design trends of tomorrow can be found in the Hyundai i-flow study. Here, too, an IMC spray skin covers the instrument panel. The concept vehicle, which Hyundai built with the assistance of BASF, was showcased for the first time at the Geneva Motor Show in March of this year. One of the targets of this concept is to present the wide array of options of the various BASF materials.
However, it is not only because of its extraordinary esthetic and haptic properties that Elastoskin is suitable for use in automotive interiors. Low emission values mean that the IMC spray skin lends itself particularly well for this field of application. A very important point regarding the safety of vehicle occupants is that the airbag integrated into the dashboard has to function reliably under cold conditions. The aromatic PU continues to exhibit very high flexibility even at low temperatures, and the material has easily passed airbag tests at minus 35 degrees Celsius [minus 31 degrees Fahrenheit].
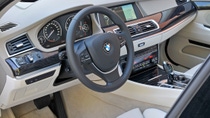
Good results in comparison to the competition
Even though aromatic polyurethanes are not lightfast and consequently require a coating, the relatively low material costs of the PU and of the coating account for the fact that they still compare very favorably to products from the competition in terms of their cost. The coating not only serves to improve the long-term durability but also plays a significant role for setting the hardness and feel, which ensues from the interplay between the PU formulation, the coating and the back-foaming system. Here, too, the coating creates a harmonious color and gloss impression over the entire surface.
Thanks to the high-grade, matt coated surface in combination with the very soft, expanded aromatic PU, Elastoskin has a very pleasant touch in comparison to TPO skin and the more conventional aliphatic spray skin. Moreover, the IMC spray skin affords considerably more design freedom than TPO does. Complex geometries are easy to form, and radii and edges are precisely reproduced without stretching the film.
In comparison to PVC slush skin, the Elastoskin spray skin not only entails advantages in terms of touch but also, and especially, in terms of multicolored design options, energy consumption during production of the component, considerably lower component density as well as interaction with the semi-rigid foam. A simple masking technique can be used to cover up individual areas of the component so as to coat them in different colors. Very light-colored surfaces can be achieved owing to the minimal interaction between the PU skin and the PU semi-rigid foam. The amount of development and testing work needed for the skin-foam material combination can be cut back considerably when an aromatic spray skin is employed.
Elastollan: Aliphatic TPU with a broad hardness spectrum
Upon its introduction onto the market three years ago, the hard-phase-modified aliphatic HPM-TPU Elastollan already attracted a lot of interest because of its multifaceted haptic possibilities, ranging from velvety to leather-like. Today, it can offer an even greater array of application options. The improvements achieved in its flow properties as well as the broad spectrum of available Shore hardness values mean that there are almost no limits when it comes to component design, to creating grain patterns and to attaining a soft touch.
The special feature of Elastollan is that its feel can be precisely set to match customer specifications and to meet the application requirements by fine-tuning the interaction of the Shore hardness value with the surface design. Components with Elastollan surfaces can be integrated into the application environment seamlessly, both from an esthetic and from a haptic standpoint.
The most recent example is the cover of the center console of the VW Golf VI, which has obtained the European SPE Award last year. In close cooperation with BASF applications engineers and the Austrian machine manufacturer Engel, the automotive supplier Key Plastics from Lennestadt, Germany, was able to develop this complex part within a very short period of time.
This center console cover is made by means of two-component injection molding with PC/ABS (polycarbonate/acrylonitrile butadiene styrene copolymer) as the underlying component. This complex component surrounds functional elements such as the storage compartment, ashtray, air-conditioner control element, rolling cover of the cup holder and chrome ornamentation on the gearshift cover. The high lightfastness of the aliphatic HPM-TPU means that there is no need for the subsequent process step of laborious offline coating. Thanks to the versatile Elastollan, the TPU soft component that runs along the contact surfaces to the adjacent parts accounts for an effective anti-squeaking effect, thus entailing yet another cost advantage since it eliminates the need for the additional vibration decoupling that is otherwise often necessary.
Another valuable advantage of HPM-TPU for use in car interiors is its resistance to creams. The soft coatings otherwise employed in offline coating processes can acquire clearly noticeable cracks over the course of time. Visible parts made of Elastollan, in contrast, retain their high-quality appearance over the entire lifetime of the vehicle. HPM-TPU is a material that easily meets the requirement for consistent component quality: Thanks to the fact that there are no coating defects that could give rise to complaints, Elastollan continues to save costs, even after the automobile has left the showroom.