Construction
Gas highway across the Arctic Circle
Our energy needs are constantly growing. To meet them reliably and resource-efficiently, we have to go new ways. New gas fields at ever greater depths extend even beyond the Arctic Circle. The Polarled gas pipeline taps previously inaccessible gas fields.
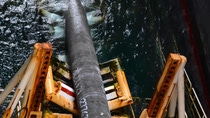
Energy consumption and energy supplies are currently controversial social issues in Europe. Our comfort and economic performance depend in large part on the security and continuity of oil and gas supplies. But natural resources are finite. Nevertheless, new oil and gas fields are now being discovered in ever deeper regions. Extraction and transport call for extreme feats of technology, materials, logistics, and personal effort. The Polarled gas pipeline of Statoil ASA has broken all records. The 482-kilometer long, 36-inch diameter pipeline extends from the Aasta Hansteen field being developed in the Norwegian Sea to Nyhamna on the west Norwegian coast. At a depth of some 1300 meters, it is deeper than all other gas pipelines of this size and the first to cross the Arctic Circle. Aasta Hansteen is a gas field of huge strategic and logistical importance for Norway. Its volume is massive, containing an estimated 47 billion cubic meters of gas beneath Arctic waters.
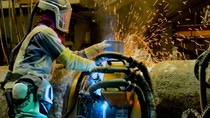
The planned production rate is also impressive: This pipeline of the superlatives has the capacity to transport up to 70 million cubic meters per day. This will only be possible, of course, given perfect conditions, since only the best and heav-iest-duty materials can withstand the harsh off-shore environment.
The field is being developed by the Norwegian company Statoil with participation of the BASF subsidiary Wintershall, which has shares in both the Aasta Hansteen development project and in the Polarled pipeline project. BASF Polyurethanes contributed the polyurethane elastomer, and laying was carried out by one of the world’s biggest pipe-laying ships, the “Solitaire” from Allseas. The gas pipeline took a total of six months to lay. Six months in which 300 pipe sections per day were supplied around the clock to the ship and subsequently processed on board, welded and checked before becoming part of the pipe string disappearing in the waters behind the Solitaire. Depending on weather conditions, between 3 and 5 kilometers were laid per day from the Solitaire.
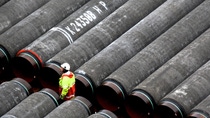
The Polarled pipeline opens up a new dimension in gas transport to Europe. Our products for infrastructure help our partners to realize such challenging projects.
The pipeline has to cover a distance of almost 500 kilometers from the gas field to the Norwegian coast. But not in a straight line. The seabed was meticulously studied beforehand so that larger rocks and reefs could be bypassed in planning the best route. All the same, this was a route that would not tolerate any error.
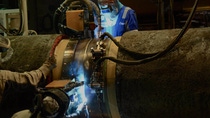
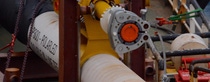
2: No pipeline in Europe’s Norwegian Sea is as deep: Polarled is as much as 1260 meters below the surface of the sea.
BASF produces a series of intelligent PU systems that reliably and sustainably protect gas pipelines – even under extreme conditions. Polyurethane is also the material of choice for superior protection of gigantic pipes. The PU Elastopor® opencell protects the pipeline from mechanical damage. External deepwater effects due to anchor movements or fishing nets are largely prevented, thus enhancing gas transport security as well as positioning the pipeline safely on the seabed. A second critical point is the prevention of corrosion at the welds. Attached to the steel pipe at regular intervals for this purpose are sacrificial anodes of a less noble metal that prevent the steel from rusting by binding electrons. Small stones are introduced into the cavities which are then filled with the compact PU elastomer Elastoshore®.
The development of the new gas fields also involves a novel Spar platform, the first and largest of its kind and the first platform of this type in the region. The gas is conveyed from the sea depths via the floating colums, fed into the Polarled pipeline and transported on toward the coast. The Polarled project is a landmark for energy supplies in the coming years and shows what is possible when superlative engineering combines with the best materials.