Performance Polymers
3 Reasons Why Ultrasim® is Indispensable for Designers and Engineers
BASF has recently expanded the application range of its Ultrasim® simulation tool.
The CAE tool now calculates component concepts based on polyurethanes and thermoplastic polyurethanes and not just engineering plastics – If you’re a developer or an engineer, this is big news for your development cycle!
Whether you work in construction, transportation, industrial manufacturing or consumer goods industries, Ultrasim® is an indispensable tool for developers and engineers who design and manufacture high-performance plastic parts. It is applicable at every stage, from material development and modeling to initial or prototype processing to the final product’s manufacture. Keep reading to learn three great reasons why Ultrasim® is the solution you didn’t know you needed.
Building Confidence
Injection molded plastics markets are growing, and with increasing demand, you need to have confidence in your production cycles and know that you’re getting things done right the first time.
High-performance plastics offer exceptional performance and easy processing, and the breadth of plastic’s properties allow for them to be used in place of other materials such as rubber or metal at a fraction of the material and production cost. But efficient development can be exceedingly complex and demanding for engineers and developers, who face challenges such as choosing the right plastic for the job, creating the proper mold designs, taking failure points into consideration, and constantly testing for issues. And this process can still be inefficient, especially if engineers are not properly calibrating their tests for plastics or if they use the same models that they would for metal components.
The truth is that industry-standard tools are not accurate enough to predict the behavior of all plastic parts, which of course confounds developers and sends them back to the drawing board, making the design phase longer and more expensive than it needs to be.
Different materials fail under stress tests for a variety of reasons. The beauty of Ultrasim® is that it can perform simulations on plastics and polyurethanes for both the initial static or crush and cyclic fatigue loads of a component, as well as giving the precise description of stress softening (the Mullins effect) during cyclic loading of thermoplastic urethanes.
Ultrasim® allows you to see the future of your product without committing the time and labor of your engineers to endless prototyping, allowing you to bypass major stages of development, delivering 90-95 percent and sometimes better accuracy when predicting the performance of parts molded using BASF materials.
The confidence that comes with knowing that your design is right the first time pays off in major ways.
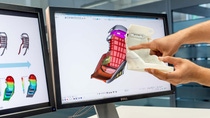
Save money in the Development Phase
Ultrasim® improves prediction accuracy, reduces development time, and doesn’t rely on average or standardized material property values, which saves money across the board.
Rather than creating prototypes first and testing afterward, your engineering team can virtually test first and then start building with greater accuracy with Ultrasim®. Using the lowest amount of mass means a considerable reduction in material cost, while bypassing development stages also means major labor and capital cost savings.
Consider the incredible uses Ultrasim® could have in automotive manufacturing, for instance. If a vehicle design is validated before development begins, this would save a company millions of dollars and hundreds of hours. An error in design could be spotted well before the prototyping stage, turning what would once have been a major roadblock into little more than a speed bump along the road to success. This was a key success factor with Toyota and their Altair Enlighten Award winning seatback.
Providing Sustainability
With improved efficiency and fewer stages in the production cycle, companies use materials in a way that is beneficial, rather than wasteful.
Ultrasim® increases development efficiency by optimizing mass for material savings thereby improving confidence in a product’s expected behavior before prototyping begins. This insight provides development teams with quick and reliable information about how BASF materials behave in their planned components during production as well as at a later stage during service life.
In summary, Ultrasim® offers insight into:
- Flow from manufacturing dynamics
- Fiber orientation
- Modelling geometry and the application of loads to predict failure
- Component concepts evaluation and differentiation based on elastomers, especially Elastollan®, BASF’s thermoplastic polyurethane
These insights along with partnering with BASF as an innovation partner, grant development teams the confidence to get the job done right the first time, saves them money on labor and material costs, and provides better sustainability thanks to the improved shelf life of products.
Contact us if you would like to discuss a project where Ultrasim® can help.