Performance Polymers
Ultradur® HR: PBT para entornos calientes y húmedos
Vida útil prolongada bajo condiciones exigentes
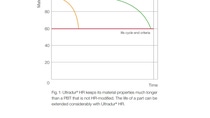
La principal característica de la gama de productos Ultradur® con el sufijo HR (=resistente a la hidrólisis) es la resistencia extremadamente elevada del polímero PBT (=tereftalato de polibutileno) a los daños ocasionados por agua a temperaturas elevadas.
El contacto con agua en los poliésteres, incluso en forma de humedad ambiente, provoca una ruptura hidrolítica de las cadenas de polímeros y, por consiguiente, un debilitamiento del material, en especial, a temperaturas elevadas.
Ultradur® HR está basado en un PBT estándar, pero incorpora aditivos altamente efectivos que retardan en gran medida la degradación hidrolítica y, por consiguiente, pueden incrementar considerablemente la vida útil de una pieza.
Demandas más elevadas para aplicaciones plásticas
Para aplicaciones críticas como las de los sistemas electrónicos automovilísticos, una larga vida útil y la fiabilidad son requisitos básicos. A menudo, es posible que la temperatura media de servicio en componentes electrónicos modernos aumente, por ejemplo, debido al compactado.
También es posible que los componentes se utilicen en lugares expuestos en gran medida al calor residual del sistema de accionamiento. Evidentemente, las piezas de plástico deben ser funcionales en todas las zonas climáticas del mundo, incluso en condiciones de humedad y calor.
Si las salpicaduras de agua y la sal para carreteras son protagonistas, los requisitos del plástico pueden ser aún mayores. Por lo tanto, el nivel y la duración del estrés son factores clave a la hora de determinar si una aplicación es viable utilizando un PBT sin resistencia mejorada a la hidrólisis.
En la actualidad, las especificaciones de varias aplicaciones de plásticos en el sector automovilístico incluyen ensayos con temperaturas elevadas y humedad, o ensayos con condiciones climáticas cambiantes. Solo los grados de PBT modificados para ser resistentes a la hidrólisis superan estos ensayos.
Ultradur® HR combines hydrolysis resistance with stable processing
Gama de aplicaciones de Ultradur®
Las aplicaciones son tan diversas como las propiedades del producto: ¡explore las diferentes posibilidades de aplicación de Ultradur®!