Automotive
Honeycomb technology for lightweight interior applications
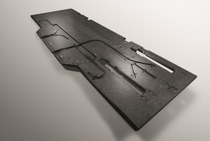
The honeycomb design found in the insect world is making its way into the auto industry, beating out man-made blow molded polypropylene in terms of strength and weight. Used within a variety of automotive components, the honeycomb structure consists of corrugated paper that is made to resemble a honeycomb. It is surrounded on either side by fiber glass sheets and a layer of polyurethane is sprayed on the top and bottom.
The reason this technology is gaining prominence is that it's extremely high strength, but also extremely low weight. It's been on the marketplace for many years, but as pressure to lightweight increases, this low risk application will continue to be used to pull weight out of the vehicle.
Reduce weight with honeycomb designs
Automakers have been making lightweighting strides using this technology in interior applications such as trunk load floors, hatchbacks and sun shades. The honeycomb design is especially popular as it allows automakers to easily reduce weight within non-safety critical applications as opposed to the vehicle's chassis applications. There is less risk of it negatively impacting its ability to absorb the impact of a crash, in addition to fewer safety restrictions.
Create exterior parts with honeycomb sandwich structures
BASF has seen a direct correlation between the greater pressure to lightweight and the amount of honeycomb load floors in the marketplace. A BASF customer was determined to take it a step further, having already used a polyurethane honeycomb structure in some of its semi-structural interior vehicle parts.
The request to BASF was to create a lighter weight roof for small city cars using the existing honeycomb structure and same Class A foil from previous roof models.
BASF rose to the challenge, creating the first exterior car part featuring honeycomb sandwich structure with a class-A film, resulting in 30 percent weight savings compared to the previous roof. To meet the demand, BASF used its Elastoflex® technology, which has multiple benefits including:
Some modifications were required to ensure that this part could meet customer needs of an exterior application, including adjusting the viscosity and reactivity of Elastoflex®. The solution can be optimally processed in each manufacturing step and shows good adhesion properties, guaranteeing uniform, thin wetting of the fiber glass mats.
The industry-leading properties of BASF's polyurethane chemistry continue to make it a top choice for Tier I suppliers and automakers when constructing honeycomb sandwich structures and the company looks forward to keeping the industry buzzing about its latest offerings.