Automotive
Innovative foam for thin and light instrument panels
- Elastoflex® E produces slim and light components for automobile interiors
- Thin-Light system wins the SPE Environmental Category Award
- Global availability with local support
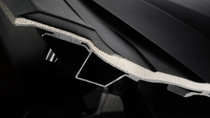
Automobile manufacturers and processors are always searching for new, cost-effective solutions for more efficient components. This imposes a variety of challenges on material suppliers. For example, highly complex instrument panels must comply with current requirements while at the same time supporting trends like autonomous driving. The complexity of this safety component is increased both by the size, design and safety requirements and by the possible incorporation of technical equipment. On top of that, the dashboard must also provide the driver with the maximum comfort and feel pleasant to use.
BASF has been supplying advanced PU foams for foam-backed instrument panels for many years. The production process involves injecting a polyurethane foam between the outer skin and the support of the instrument panel, bonding the surface and support material together. The foam produces a material that has a very soft haptic. These customized systems are attractive because of their low emissions and offer optimum adhesion to surfaces produced from a wide range of materials. Even PVC skins can be processed easily.
Bio-based foam delivers weight saving
A new series of systems in the Elastoflex® E product group now allows significant weight reductions and foam densities of around 120g/L without sacrificing any of the unique characteristics of these foams. Up to 30% of the foam weight is saved, depending on the component geometry. With its very robust and fine cell-structure, this Thin-Light system can be used for components with a much smaller profile of less than 5 mm. This results in very light and thin instrument panels or door elements, which offer scope for new design options. This latest addition to BASF’s portfolio meets strict requirements and creates a flexible offer to help its customers towards a mobile future.
The new PU systems save weight, and are designed to incorporate sensors or control elements. We've also managed to reduce the emission values even further and simplify the use of lasers for airbag weakening.
As part of this new generation of systems, BASF has also developed a foam system based on renewable raw materials. Elastoflex® E 3496/102 uses castor oil as a renewable raw material and can be used to produce complex components that are both light and thin with excellent adhesion to a wide range of surfaces. This successful development was awarded the SPE Environmental Category Award at the end of 2017. The project shared the prize for sustainable innovation with International Automotive Components (IAC).
With the new Thin-Light systems, BASF is expanding its global portfolio of PU foams for instrument panels, doors and armrests.