Automotive
Touch it, feel it - Haptex®
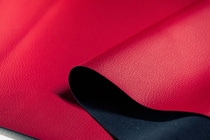
The driving experience and comfort plays a significant role and goes parallel with the trend for longer time we stay in a car. It is the overall target of every automotive interior designer to create an impression of pleasure, fun and fascination, while comfort and safety must be at the highest levels. BASF has a strong portfolio of all kinds of materials meeting these requirements of the future.
One of the latest inventions deals with providing a polyurethane system for synthetic leather that beats all other available solutions in terms of durability, comfort and safety by the development of Haptex®. BASF material solution Haptex® enables synthetic leather producers to create a high comfortable leather without the use of any solvents and without need of large water consumption. Consequently, emissions and exceptionally odor of these new synthetic leathers made with Haptex® are significantly lower compared with established solutions in the market, giving not only benefits to comfort but also to health of passengers.
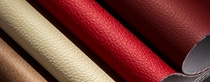
BASF also took special attention to improve mechanical properties for synthetic leather made by Haptex® which can be seen especially in a very high peel strength, abrasion resistance and high flexing resistance even at cold temperature down to -30°C. Since Haptex® has no need for any plasticizer or solvents, the material properties remain unchanged. Even at low temperatures the material remains flexible. While other synthetic leather products need a multitude of stabilizers and dispersing additives, Haptex® based PU leather does not need these additives. This makes it an excellent choice for Instrumental-, door, armrest or mid console covers, but also for seating, steering wheel or gear covers with strong requirements to mechanical stress. Haptex® simplifies the production processes and optimizes costs when manufacturing instrument panels made of synthetic leather as it eliminates the conventional wet process step and the use of adhesives in the dry process step.