Construction
Business Building with PU Sandwich panels
Building Sustainably with PU Sandwich Panels: New Construction Method and a Proven Material
Contemporary construction has to satisfy a whole range of requirements. For a project to succeed, it’s essential to get the design, materials, sustainability, esthetics and costs right. So it makes sense to try out new things for a change. A solid wooden house, for example, with a complete shell of polyurethane (PU) sandwich panels. In Buttenwiesen in Bavaria, an exciting private house with plenty of space for commercial uses has been built in this way. Fully insulated with Elastopir® PU panels from BASF.
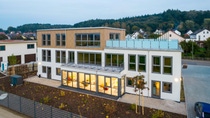
Dependable quality: Sandwich panels containing PU
Insulating buildings with polyurethane is not in itself new. Sandwich panels made of PU rigid foam have been in use on warehouses and industrial buildings for decades. The material has a lot going for it. Construction elements with a core of rigid polyurethane foam such as Elastopor® and Elastopir® are ideal for the production of facade and roof elements of industrially used buildings. They optimally combine outstanding mechanical and physical properties with thermal insulation. As the core material of multi-layer elements with diffusion-tight metal facings, they are used on industrial shed, cold store and warehouse buildings.
Rethinking insulation: Innovative mix of materials
In the construction of private houses, there has so far been less interest in using PU construction elements – something that Werner Fech, an entrepreneur from Buttenwiesen, decided to change. Together with panel manufacturer Romakowski GmbH and BASF, he has put up an impressive solid wood building with a complete exterior facade of PU. The innovative project thus combines sustainable materials with high-quality PU insulation products such as Elastopir®.
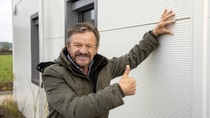
No one has previously attempted this mix. It always takes a dose of entrepreneurship and companies that can make it happen.
The new building is functional and fits perfectly into its surroundings. A complete glass frontage extends to the west, and to the east there is a semi-oval glazed facade. The building’s uses are also mixed. The ground floor, with its large glazed surfaces, provides bright and warmly designed premises for a dental practice. On the second floor, there will be a firm of investment consultants along with a showroom and an office for energy advisers. In another part of the building, the client himself will then move in with his Timber Systems business headquarters and the attached research laboratory.
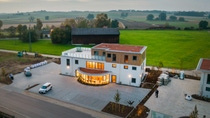
Greater sustainability: Solid wood construction combined with Elastopir®
The building features an intelligent mix of commercial and office space. Above all, however, the construction method introduces a novel combination. The basis is an inner shell of solid wood, with all the positive features of the natural material. The interiors are cozy, with an appealing esthetic and outstanding acoustics. Together with the large expanses of glazing, they also have a bright, modern and functional aura. Wrapped around the wooden cube is the exterior facade of polyurethane sandwich panels.
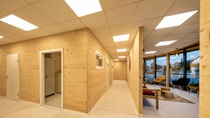

These were supplied by BASF’s long-standing customer Romakowski GmbH in Buttenwiesen. The owner-managed firm specializes in sandwich panels for industrial shed and cold store construction. Building owner Fech’s goal was to have a maintenance-free facade that needs neither painting nor rendering, but looks attractive all the same. A solution was quickly found for this as well: “We’re highly flexible in the design of our panels,” explains Christian Romakowski, 3rd-generation owner of the family business. “The wall elements we’ve used here have a newly developed dark wood color and a wood grain surface structure.” In Buttenwiesen, two different colors, white and the darker wood tone, have been combined on the exterior panels. Visually, these establish a link with the interior while enabling the facade to blend in with its surroundings and the neighboring buildings.
The PU sandwich system enables environmentally friendly construction and big potential for energy savings. Building with these construction elements is particularly cost-effective, as they are prefabricated in the plant and supplied ready for installation. For the building owner, this means efficient planning in terms of costs and time management. The decisive advantage, however, lies in the PU panels’ outstanding insulation performance. Christian Renner, BASF Performance Materials Construction, knows the products inside out: “Our Elastopir® system, the core of the construction elements, makes highly energy-efficient construction possible. It features extra-low thermal conductivity and also delivers maximum safety in terms of fire protection.”
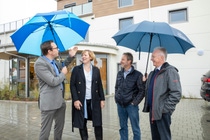
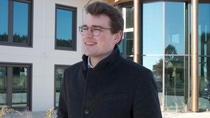
Innovation and smart ideas are the only way we can meet the challenges of environmental protection and climate-friendly construction.
Far from being a contradiction in terms, solid wood combined with sandwich construction shows how forward-looking, sustainable building can work. The result is a state-of-the-art structure that unites highly efficient insulation and multifunctional interiors with the atmosphere of traditional natural materials. Romakowski is convinced that projects like the recently completed office building in Buttenwiesen are the future of construction. So it’s a good thing there are pioneers and companies willing to pool their expertise and develop innovative materials.
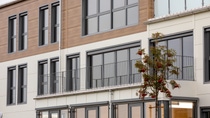
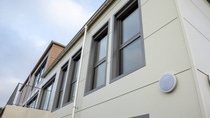