Performance Polymers
How spray transfer molding helps to create lighter, stronger automotive exterior components
New technologies allow automakers to use lightweight composite materials that meet their performance and design needs in more areas than ever before.
When it comes to the automotive industry, the future is electric: a recent study predicts that electric vehicles will hit 28% of global passenger vehicle sales by 2030, rising to 58% in 2040. The projected increase stems from price parity with internal combustion vehicles, as well as improved batteries and charging infrastructure availability.
To facilitate this shift, automakers are investing in new technologies to make their vehicles lighter and improve their power-to-weight ratio, enabling them to go farther and faster. These weight savings can come from almost any part of the vehicle, from load floors and centre consoles to body panels and roofs.
Previously, exterior automotive components were made from heavier metals such as steel or aluminum, which provide strong durability at the cost of increased weight.
Now there’s a better option. Manufacturing composite components using atomized polyurethane in a process known as spray transfer molding (STM) is an efficient way to create strong, lightweight interior and exterior automotive components in nearly any design or shape.
As an early adaptor in new technologies with a long history of expertise in the automotive performance materials market, BASF has the capabilities to bring an idea from concept to production with the right designs to match OEM specifications.
Why use spray transfer molded composite materials?
Spray transfer molding is a process where atomized polyurethane particles are sprayed onto a non-woven material with a high-pressure nozzle, then molded into the desired shape, providing a rigid, lightweight design.
“Spray transfer molding typically uses a fabric supported by a core material such as paper, foam, metal or polymer, which is then overlayed with a fiber reinforcement and sprayed with a two-component polyurethane system,” says Michael Barry, Market Segment Manager at BASF. “Next, it’s put into a press that molds it to the final shape as the polyurethane cures, and the result is a component that's very stiff and light relative to other solutions.”
These lightweight parts add structural integrity in areas where other materials, such as steel or aluminum, may be too heavy or costly. A polyurethane load floor made with STM, for example, can weigh up to 50 percent less than one made with heavier polypropylene without sacrificing performance.
STM inside and out
Although spray transfer molding has been used to create interior automotive components for some time, the list of applications where it can be used the vehicle’s exterior is growing quickly. In the interior space, STM is commonly used to create components such as package trays, door panels and sunshades.
“We're just now starting to scratch the surface for potential exterior applications,” says Barry. “Applications that we're looking at include reinforcements for body panels and tailgates, tonneau covers and underbody panels — things with relatively simple geometry but where low weights and stiffness are highly desirable properties.”
Exterior components must also be able to withstand the rigors of nature and daily wear-and-tear to be effective and provide longevity. Although the paper core itself isn’t resistant to water, the surrounding fiber reinforcement and polyurethane provide an extremely tight seal, along with structural integrity, to ensure no failures occur.
“The components we've made perform really well with impact testing against stone impacts or other debris from the road,” says Barry. “They also have strong chemical resistance, and the typical exposure to salt, fluids, oils or other debris isn't really a problem for this type of material.”
Aside from technical strength, the aesthetic for automotive exterior components must look the part as well. Automakers need their parts to flow seamlessly and match the color and design expected by consumers. In-mold coating, or RIM application, can be seamlessly integrated in the process, which enables manufacturers to achieve excellent “Class A” exterior surfaces on components made with STM.
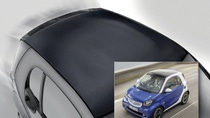
A more sustainable solution
The positive effects of lightweighting shouldn’t be understated. Experts project that for every 220-pound decrease in the weight of a vehicle, there will be an associated 3-5% decrease in carbon emissions depending on total vehicle size and powertrain type.
In addition to the increased fuel efficiency achieved by lightweighting, the ability to incorporate natural renewable fibers is another benefit of spray transfer molded components. BASF’s Elastoflex® polyurethane is composed of a high percentage of castor oil, a bio-renewable resource derived from the ricinus communis plant native to tropical areas of Africa and Asia.
“We’ve focused on developing polyurethane chemistries that have in part come from bio-renewable resources,” says Barry. “We've also done quite a bit of development incorporating natural fibers, like jute.”
Jute fibers are an environmentally friendly natural material produced from jute plants in the genus Corchorus, family Malvaceae, and can deliver strong tensile strength of 104.9 ± 8.8MPa when treated.
On the road
There are already some cars on the road today that make use of spray transfer molded components for their exteriors. The Mercedes Benz Smart Fortwo is an example of this technology in action, employing a honeycomb sandwich structure with a class A film that’s 30% lighter than the standard roof on the previous model.
“BASF has taken a position of leadership, pushing the possibilities that spray transfer molding can offer for these exterior applications,” says Barry. “We've learned a lot and we’re continuing to develop the chemistry and the processes to make it easier and more cost effective to implement STM on a broader scale in other applications, as well.”
As an industry leader, BASF provides expertise and assistance to auto parts makers looking to create concepts and test designs for spray transfer molded components. With BASF’s state-of-the-art lab in Wyandotte, Michigan, customers can design, build and test their ideas and bring them to life, allowing them to test the feasibility of a design with minimal risk and investment.
“We can take an idea from a concept to production, with both the resources and experience to make sure the chemistry works, as well as the manufacturing capability to test it before significant production investments are needed,” says Barry. “Five years from now, I think we'll have multiple examples of commercially available exterior solutions using spray transfer molding technology.”
For more information on BASF’s spray transfer molding capabilities, click here.