Performance Polymers
Spray transfer molding introduces new composite capabilities for automotive applications
New innovations are helping to grow the list of automotive components that can be made out of lightweight and sustainable composite materials
As calls for sustainability across industries continues to grow, automakers are rushing to improve fuel efficiency in their vehicle lineup for an increasingly demanding consumer market.
The most common method of improving a vehicle’s fuel economy is through lightweighting, a process which looks at ways to reduce a vehicle’s overall weight to improve power-to-weight ratio and fuel efficiency.
Previously, interior automotive components were typically made from polypropylene, a thermoplastic polymer which is usually injection-molded to form the desired shape. Now, however, more automakers are looking towards composite components made using polyurethane, a lighter, more flexible polymer that can be applied via spray transfer molding (STM) to create strong, lightweight designs in almost any shape.
As an innovator in composite technologies, BASF is committed to helping manufacturers improve fuel efficiency in their vehicles through lighter, stronger and more sustainable composite-created components.
Composite composition
A composite material is composed of two or more dissimilar elements that are formed together, retaining their individual mechanical properties to create a material with new advantages such as improved strength or structure. In automotive applications, composite materials are useful due to their excellent strength-to-weight ratio and flexibility.
“When we create an automotive composite, we're cutting two pieces of non-woven materials and ‘sandwiching’ them together,” says Jeffrey Hagar, Market Segment Manager at BASF. “Then for the spray transfer molding process, we're going to spray polyurethane onto the non-woven material and add heat and pressure, and that's what provides the required geometry.”
For increased strength, a typical automotive composite material is usually composed of a fiber honeycomb structure which is then sandwiched between two layers of glass fibres with polyurethane applied. The “I-beam” principle from the honeycomb shape disperses the load evenly and with minimal added weight.
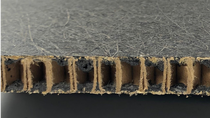
Why spray transfer molding?
Spray transfer molding is the process of spraying atomized polyurethane with a high-pressure nozzle onto the non-woven material to give it a rigid, lightweight shape that can be flexibly molded to a desired design.
Spray transfer molding provides some advantages over traditional application systems such as injection molding or pultrusion, including a shorter dry time, homogenous distribution, an anti-drip formulation for reduced material usage and lower maintenance, and a lower overall weight.
“We use composite technology to provide that weight reduction,” explains Hagar. “For example, in a polypropylene load floor versus a polyurethane composite load floor made with STM, we were able to pull about 50 percent of the weight out of the load floor. This is really attractive to the automaker because it didn't have any impact to safety, so it's a really low-risk and a low-cost change to the vehicle.”
Localization is another capability of spray transfer molding, allowing manufacturers to add additional polyurethane in one focused area, avoiding the need to make the entire component thicker.
Beyond the load floor
Spray transfer molding and composite technology is already commonly used to create lightweight vehicle load floors for SUV cargo areas and trunk liners, but that’s just the beginning of the possibilities. Typically, the farther away from the center of gravity, the more valuable the weight savings.
Other applications where spray transfer molding can be used includes center consoles, package trays, door panels, sunshades and hatchbacks, with more even applications coming down the line.
“The biggest misnomer in the marketplace right now is that polyurethane composites can only be flat,” says Hagar. “We're able to get almost a 90-degree angle out of it, we’re now capable of geometry freedom and that's what the market does not always understand.”
Substrate-only spray transfer molding is a process that allows manufacturers to spray polyurethane directly on a nonwoven substrate without the need for the honeycomb structure. Applications using this method include integral skins, seating, semi-structural parts, and acoustic components.
Since many of these components were previously made with heavier plastic or metal, the opportunity to greatly reduce their weight is extremely attractive to manufacturers who are looking to cut weight wherever they can.
“Spray transfer molding is an excellent process for many applications beyond simple load floors,” says Hagar. “We have a strong market presence in that area, but we’re also looking at more and more alternative uses for this technology.”
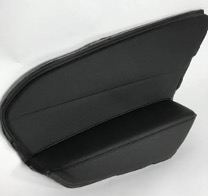
Sights on sustainability
To coincide with the demand for sustainable solutions, BASF’s Elastoflex® polyurethane is composed of a high percentage of castor oil, a bio-renewable resource derived from the ricinus communis plant native to tropical areas of Africa and Asia.
“The best part about castor oil is that where these castor plants are grown, the only thing that grows there is castor, so it's not part of the food supply,” says Hagar. “We're pulling petroleum-based material out of the polyurethane and we're putting biorenewable content in, and then we're going to spray that onto natural fibers. We're capturing a lot of the green initiative that's being requested from the automakers.”
Natural fibers like bamboo or jute can be used to create the honeycomb shape and offer good strength and energy absorption with a similar stiffness to conventional glass fibers. Unlike glass fibers, however, these natural fibers are renewable and deliver superior flexural behavior in stress tests. Together with castor oil, these fibres contribute to lowering the carbon footprint of the vehicle manufacturing process.
Getting started with spray transfer molding
One of the hurdles to implementing widespread spray transfer molding capabilities is accessing the proper equipment to design and test composite components made with spray transfer molding.
BASF has introduced a state-of-the-art Customer Innovation Center in Wyandotte, Michigan to help customers design, build and test concepts and ideas before bringing them to market. BASF also provided support and technical support for users who require assistance.
“We realized that one of the problems in the market was that customers do not necessarily have the equipment to make spray transfer molded components,” says Hagar. “The Innovation Center is for customers to come in and use, to build anything it is that they want free of charge and to actually be able to make a functional prototype part to take to their end customer. We want them to be able to win in the marketplace before production equipment is required.”
This unique approach allows customers to design protypes with very little investment required, and also allows for collaboration between different teams; for example, a manufacturer can work with chemists and glass or fiber suppliers to determine the best solution for their application.
What’s next?
With the automotive industry continuing to move to lightweight fuel-efficient or electric vehicles, components made with low weight composite materials are only going to become more and more common.
Weight savings of 20-50 percent have an enormous potential to decrease a car’s fuel emissions, and the technology has caught the eye of almost every automaker worldwide. With advances in spray transfer molding and composite technology, the list of applications that can benefit from this process keeps growing.
“In the coming years, spray transfer molding and composite materials are going to rapidly replace metal and plastic,” says Hagar. “They’re going to lower cost and reduce weight, and they’re going to give developers more design freedom and flexibility.”
For more information on BASF’s spray transfer molding capabilities, click here