Automotive
Poliamidas optimizadas contra impactos
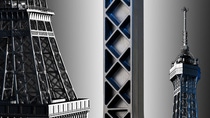
Torre Eiffel Retorcida
Los dos primeros grados se denominan Ultramid® B3ZG7 CR y Ultramid® B3ZG3 CR, reforzados con 35 o 15 por ciento de fibras de vidrio. El tercer grado es Ultramid® B3ZG10 CR, la primera poliamida 6 modificada por impacto de BASF con un 50 por ciento de fibras de vidrio. Inicialmente destinados a aplicaciones corporales con miras a proporcionar protección a los peatones, estos plásticos de alta resistencia también son adecuados para otros componentes relevantes para choques en el vehículo, en el volante, como inserciones estructurales o en los asientos: dondequiera que se absorban rápidamente grandes cantidades de energía se requiere. En comparación con su predecesor de la familia CR, ofrecen una resistencia al impacto aún más mejorada. Las cantidades comerciales de los tres grados están disponibles de inmediato.
Para el desarrollo de materiales y propósitos de prueba, BASF desarrolló una muestra de prueba de torsión y flexión específicamente para las nuevas calidades optimizadas para impactos. La muestra de prueba, que se puede utilizar para pruebas en clientes, recuerda a la Torre Eiffel de París y tiene nervaduras de 45°. Mientras que el material CR clásico Ultramid® B3WG6 CR ya se puede distorsionar en casi 150° en las pruebas de torsión estática sin romperse, los nuevos grados resisten la distorsión por el enorme ángulo de hasta 240° sin sufrir daños.
Apenas hay otra clase de material en el mercado que pueda soportar tal carga y permanecer intacta. La topología de la pieza sobre la que se realizaron estas pruebas se optimizó en vista de la capacidad de carga mediante la herramienta de simulación ULTRASIM™ universalmente aplicable de BASF. Con esta muestra de prueba, la empresa puede realizar pruebas de flexión de un solo punto y de tres puntos además de la prueba de torsión. Al mismo tiempo, la caracterización de un material en particular se puede validar en esta muestra de prueba para su optimización por ULTRASIM™.
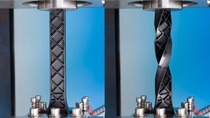
Cada vez más especialidades - la familia Ultramid B CR
Los tres nuevos grados de la familia Ultramid® CR son especialidades en la línea de formulaciones compuestas de poliamida 6. Son ideales para absorber rápidamente una gran cantidad de energía en situaciones exigentes. Mientras tanto, lo que se ha convertido en una aplicación casi clásica es el llamado LBS (refuerzo inferior del parachoques), una gran pieza Ultramid que Opel utiliza como elemento de refuerzo debajo del parachoques delantero para la protección de los peatones, y cuyos requisitos se vuelven más exigente de modelo a modelo. "Ayudamos a los clientes que utilizan estas especialidades de alto rendimiento a diseñar sus piezas con nuestro paquete de servicio ULTRASIM™", explicó Andreas Wüst, experto de CAE en plásticos de ingeniería en BASF.
Los tres productos se desarrollaron como un sistema modular con propiedades a medida y, según los requisitos, ofrecen al cliente una versión algo más blanda o más rígida. "Esto hace posible jugar con la geometría, la rigidez y la tenacidad, permitiendo que las piezas tengan una acción de resorte más rígida o más suave", continúa Anka Bernnat de marketing técnico. Con todo, los tres plásticos ofrecen una mejora en la elasticidad de hasta un 200% y hasta un 50% más de rigidez. Las piezas estructurales que deben satisfacer los requisitos de impacto, como las que ya se requieren para la protección de los peatones, se pueden fabricar entre un 20 y un 30 por ciento más ligeras cuando se explota todo el potencial de estos materiales.