Automotive
Driving forward plastics solutions for chassis, structural applications, and body in white
The automotive chassis is roughly one third of the mass of vehicle and forms the structure where the interior, exterior, powertrain, and electronics finds mounting. It is the first defense in protecting the occupant and components protection. The incumbent materials are primarily metal based offering an opportunity to use composites to reduce weight and enhance performance (strength, energy management, NVH damping, etc.) with our expanding product portfolio.
Watch the video on the right to get an overview on our chassis, structural applications, and body in white solutions.
Our solutions
» Applications
Versatile applications for automotive chassis and body in white solutions
Whatever your specific needs for the variety of different chassis and BIW solutions are: BASF connects new material developments and services in order to create system solutions which give your chassis and BIW solutions the distinctive advantage.
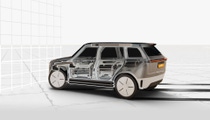
Occupant and future powertrain protection
eMobility is the lead movement in the automotive industry to address our need to make our lives more sustainable. Due to the size and location of the batteries it is imperative to protect the passengers by limiting the intrusion into the battery compartment during an impact event. Continuous fiber systems using our polyurethane Elastocoat® offers the ability to create structures with the strength of steel at third of the mass with no concern of mixing with dissimilar materials. In addition to offering structure, BASF offers solution to manage kinetic energy for high deformation events with our Ultramid® in the form of foams or impact modified injection or extruded grades.
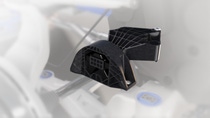
Noise and vibration management
eMobility brings additional challenges to noise and vibration abatement. Electric motors reduce vibration at lower frequencies but introduce new higher frequency noises due to the high rpm motors. BASF Ultramid® reduces sound and vibration transmission when replacing metallic engine suspension mounts due to the inherent damping characteristics of polymers. BASF Elastoflex® ultralight BIW NVH foam is used today to fill the cavities of the automotive body to absorb and block noise transmission to the automobile interior. Cellasto ® microcellular polyurethane elastomers are used in chassis and suspension applications to isolate vibrations and reduce structure-borne noise. Their superior damping behavior across a wide frequency range makes them ideal for managing NVH challenges in electric vehicles.
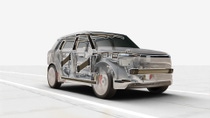
Lightweight body structure enhancement
To improve the performance of metal structures, BASF’s Thermoplastic Ultramid® and Ultradur® is used to reinforce the metal profiles by delaying the failure of metal structure leading to an increased peak load up to 300%. This can also be accomplished by filling the cavity with BASF Elastolit® D structural foam.
Explore more
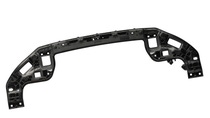
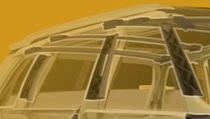
Sustainability
As the world moves to a sustainable and circular economy, BASF is supporting car manufacturers and suppliers to the automotive industries achieving their respective goals. BASF products & support are driving lightweight implementation, leading to lower raw material usage and reduced fuel consumption. We provide transparency, as we have mapped the CO2 consumption of over 45,000 of our products. Furthermore, our Sustainability Toolbox offers concrete possibilities to lower the CO2 footprint of our and your products further, as well as to increase circularity. Eager to learn more? Just follow the links below.
Learn more about our sustainable plastics solutions for the automotive industry
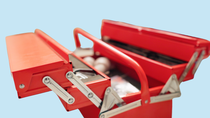
Detailed material information for chassis, structural applications, and body in white solutions
Polymer based solutions create an automobile chassis to manage the high out propulsion, to maximize occupant protection, reduce vehicle mass, and improve passenger comfort.
The emergence of eMobility brings new challenges to the chassis to provide mounting for the high torque eMotors, protect the passengers and high-density battery from intrusion during an accident, and minimize sound and vibration from these much higher frequency sources. BASF’s Polyurethanes Elastocoat®, Elastoflex® E, Elastoflex® W and Elastolit®; along with Engineered Plastics Ultramid®, Ultramid® Expand, and Ultradur® provide solutions with a superior strength to weight ratio compared to metal, manage frontal and side impact events, while providing an environment which the passenger remains in peace.
» Engineering Plastics
Our Engineering Plastics for chassis, structural applications, and body in white solutions
» Polyurethanes
Our PU systems for chassis, structural applications, and body in white solutions
» Specialty Elastomers
You would like to optimize your part performance and mass with a BASF composite solution?
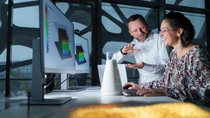
That is where part geometry, part manufacturing process, and material selection need an integrated approach. With Ultrasim® we offer you versatile and flexible CAE competence for your innovations using BASF plastics. Our analysis of component concepts on a virtual basis starts with your manufacturing process to understand the material behavior in the finished component, this is coupled with the appropriate materials and detailed material models, ranging from the virtual prototype and ideal manufacturing process to the finished mass-produced component.