Automotive
Sustainable plastics solutions for the automotive industry
By 2025, it is expected that there will be 104 million cars produced in the world annually. At the same time, awareness of the need to protect our planet increases. Sustainable mobility is an immense challenge we must take on. This too is emphasized by the expected development of the legislation affecting the industry.
Ambitious CO2 fleet management, not only considering the use phase but also in the manufacturing of a vehicle, has become a focal point for engineers in product development. In addition, recycling targets must be met, which include end-of-life recycling strategies as well as use of recycled materials already in today's car production.
Stakeholders are now driving the transformation towards a Circular Economy. BASF works with customers, both TIERs and OEMs, to provide sustainable products and solutions which help to achieve their sustainability targets and market differentiation.
Our commitment
We are fully committed to drive sustainable automotive innovations forward by partnering with players throughout the entire automotive value chain. Pilot projects as a pre-requisite towards commercialization of our offering are state of the art. Furthermore, BASF is an active member in various networks to develop and establish sustainable solutions and processes in the automotive industry.
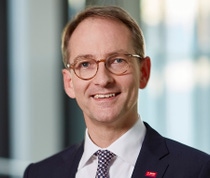
At BASF we actively drive future trends and find smart answers for the world’s challenges. We are strongly committed to create sustainable solutions for our automotive customers, jointly exploring endless possibilities and helping them to achieve zero emissions.
Read more about pilot projects with Tiers and OEM, our engagement in the Catena-X Automotive Network and more:
Check our sustainable plastics solutions for the automotive industry
Only together we can find answers to the crucial questions that drive forward sustainable automotive solutions and production processes.
How can I reduce CO2 upstream and in the production phase?
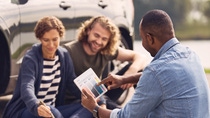.jpg)
The reduction of CO2 emissions is a crucial point for all plastics manufacturers in the production process. In addition to mechanical recycling, BASF introduced chemical recycling in 2018. Together with our partners we developed the pyrolysis technology which turns plastic waste into a secondary raw material called pyrolysis oil. We feed the oil into BASF’s Verbund production at the beginning of the value chain, thereby saving fossil resources.
How can I reduce CO2 in the use phase?
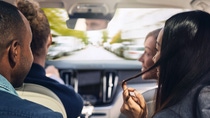
A broad BASF plastics portfolio for the automotive industry provides solutions to reduce CO2 emissions in the use phase. The functional integration by automotive plastics leads to less parts in the car and thus to a significant reduction of weight. Lightweight constructions subsequently lead to less emission and/or more energy efficiency. Furthermore, we provide you with a dedicated portfolio to meet engineering ambitions for alternative powertrains.
How do I meet ambitious recycling targets?
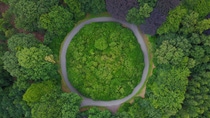
The automotive industry is facing ambitious recycling targets. A circular economy aims to decouple growth from resource consumption and is regenerative by design. As technology open partner to the automotive industry, BASF leverages mechanical as well as chemical recycling to support the industry on its transformation from linear to circular economy.
A combination of both reycycling methods will enable circular economy for all plastics in the automotive industry.
How can I substitute fossil resources by renewable resources?
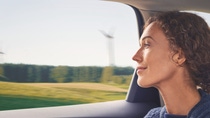
A BASF portfolio of bio-based solutions is available using castor oil as renewable compound. As part of a new generation of systems, BASF has developed a foam system based on renewable raw materials. Elastoflex® E uses castor oil as a renewable raw material and can be used to produce complex components that are both light and thin with excellent adhesion to a wide range of surfaces. Also for Ultramid® S Balance the sebacic acid, originates from the castor oil plant.
How can I quantify the carbon footprint of my products?
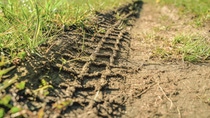
As a plastics supplier at the heart of the automotive value chain, BASF supports its customers – wheather TIERs or OEM's – in quantifying their product carbon footprint (PCF). Depending on their needs, we support our customers with multiple methods to determine the PCF. In addition, we are actively involved in various projects and alliances to quantify and to digitalize carbon footprints across the whole automotive value chain.
Comfort meets sustainability. Our innovative ways to make PU recyclable
BASF presents a new generation of flexible PU foams suitable for thermoplastic recycling at the end of their life cycle. These new meltable PU foams combine the advantages of recyclability with the comfort properties of conventional PU foams.
The foams can be 100% recycled and used as a raw material for new foams.
BASF works hand in hand with its partners to co-create solutions that address complex challenges and drive innovation and sustainability forward.
Meet your sustainability experts
Europe
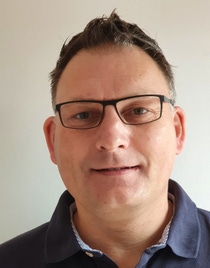
Oliver Geiger
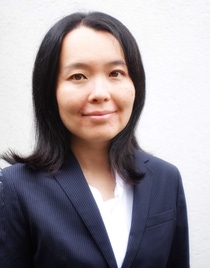
Rie Kaneko
Asia Pacific
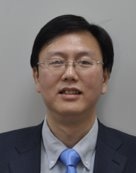
North America
South America
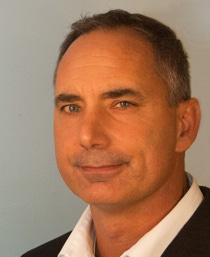
Christopher Korson
Mohamed Bouguettaya
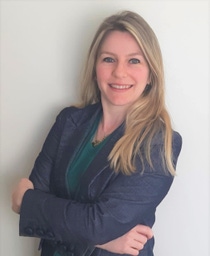
Camila Montebelli Almeida